1.
INTRODUCTION AND OBJECTIVES
1.1 Purpose
The Source Inspection Guidelines for Local Agencies (SIGLA) has been prepared to aid California local agencies to create a satisfactory Quality Assurance (QA) Source Inspection program. The term “local agency” used throughout this document means any public entity (federal, state, regional transportation planning agency [RTPA], county, city, or other local government entity) that sponsors or administers a construction contract on the state highway system. In addition, any private entity that sponsors or administers construction contracts on the state highway system, unless otherwise noted, can be considered a local agency.
Local revenues for state highway projects may include local sales tax, other local funds, local federal-aid funds (Surface Transportation Program [STP], Congestion Mitigation Air Quality [CMAQ], Transportation Enhancement Activities [TEA], and other funds), and private funds. Local agencies may combine their local funds with state and federal funds (State Transportation Improvement Program [STIP], Interregional Improvement Program [IIP], State Highway Operation and Protection Program and Minor Projects [SHOPP and Minor]) to develop transportation improvements.
This guideline document provides information on QA Source Inspection definitions, processes, procedures, roles and responsibilities, and documentation which are required in order to receive federal-aid and/or state funds for many types of local transportation projects.
These guidelines are based on Caltrans’ own QA Source Inspection practices and procedures that were carefully developed to meet federal law. These practices and procedures are outlined in the Office of Structural Materials Quality Assurance and Source Inspection (QASI) Manual which can be viewed at: http://www.dot.ca.gov/hq/esc/Translab/OSM/agencyresources.htm
1.2 Background
The passage of Senate Bill 45 in 1997 substantially changed the process by which state and federal transportation funds are allocated, placing the majority of responsibility for planning and prioritization of project funding in the hands of local and regional agencies.1 A result of these changes can be seen in the recent upward trend of projects within the State Highway System (SHS) that are Advertised, Awarded, and Administered (AAA) by external Implementing Agencies.
The California Department of Transportation (Department), as owner/operator of the State Highway System (SHS), has the statutory and inherent obligation to ensure that all modifications or additions to the SHS, regardless of project sponsor or funding source, are:
- Safe, operational, maintainable, compatible and of good value.
- Providing for the efficient multimodal movement of people and goods.
- In the best interest of the general public.
- Developed and constructed in compliance with laws and regulations that govern the use of State and Federal transportation funds.
- Developed and constructed in partnership with vested stakeholders.
Projects on the SHS shall comply with applicable state and federal standards to ensure system-wide consistency with operational, safety, and maintenance needs. The Department may approve exceptions to this requirement that it determines to be appropriate per Government Code 65086.4.
Under Title 23, United States Code, and the Joint Stewardship and Oversight Agreement between FHWA and Caltrans, Caltrans is responsible for the administration of federal-aid (FHWA funded) transportation projects in California and cannot delegate this overall administrative responsibility.
Per the Joint Stewardship Agreement, Caltrans will exercise its FHWA assumed authority by further delegating federal authority to local agencies to the greatest extent possible and for those projects advertised, awarded, and administered by the local agencies on the State Highway System, Caltrans will ensure that state standards and project development procedures are followed. The act of ensuring is also referred to as oversight.
Although Caltrans has the overall administrative responsibility, many project functions such as quality assurance during the construction phase is typically delegated to the local agencies. The legal document that outlines this delegation is called the Cooperative Agreement. This is further outlined in Deputy Directive 23 Revision 1 (DD 23 1R), which states that when external Implementing Agencies administer a project on the SHS, they are responsible for implementing adequate quality assurance procedures to ensure project components comply with Caltrans policies, standards, procedures, and best practices.
1.3 Source Inspection
Title 23 Code of Federal Regulations (CFR) Section 637.205 provided in Appendix 1 requires that each State Transportation Department (STD) develop a quality assurance program. Section 637.207 mandates that the quality assurance program has an acceptance program that includes verification sampling and testing. This testing is to be performed by qualified testing personnel employed by the STD or its designated agent, excluding the contractor and vendor.
Verification sampling and testing of materials manufactured or fabricated away from the jobsite is known as quality assurance source inspection. Section 10 of this document provides detailed information on material sampling and testing from the source.
Source inspection is an integral part of an effective QA Acceptance Program. Verification source inspection helps to ensure that structural materials incorporated into the SHS comply with contract requirements with regard to raw materials, fabrication processes, personnel certifications, and in-process QC testing. The purpose of verification source inspection is to:
- Verify that adequate off-site QC is in place
- Perform verification sampling and testing of representative material
- Perform necessary in-process verification inspections
- Perform Non-Destructive Testing at appropriate times
- Mitigate issues before the material is shipped to the jobsite
- Decrease the potential for project delays that verification sampling at the jobsite may cause
Per Materials Engineering and Testing Services and Geotechnical Services (METS/GS) Directive - 03 provided in Appendix 2, METS does not provide laboratory testing or source inspection services for construction projects administered by external Implementing Agencies on the SHS. For projects that are advertised, awarded, and administered (AAA) by external implementing agencies, source inspection shall be performed by that agency and Caltrans serves in an oversight capacity.
1.3.1 Construction Procedure Directive (CPD) 08-5
Per Caltrans Construction Procedure Directive (CPD) 08-5 (Appendix 3), and Deputy Directives 23-R1 and 90 (Appendix 4), when an agency other than Caltrans is providing verification source inspection, the Implementing Agency is required to prepare a Source Inspection Quality Management Plan (SIQMP). Approval from the state materials engineer is required for each SIQMP, prior to issuance of the encroachment permit for construction.
The SIQMP Outline has been developed to help local agencies manage their source inspection efforts when administering construction projects within the SHS. If the implementing local agency proposes to perform its own source inspection, they are required to prepare a separate SIQMP.
The SIQMP Outline is posted on the METS website and provided in Appendix 5:
http://www.dot.ca.gov/hq/esc/Translab/OSM/agencyresources/SIQMP_Outline.pdf
This guideline document is a great tool to help the local agency develop a satisfactory SIQMP.
Sample SIQMPs are also posted on the METS website and provided in Appendix 6:
http://www.dot.ca.gov/hq/esc/Translab/OSM/sampleSIQMP.htm
Back to Table of Contents
2.
REFERENCES
Local Agency resources from FHWA and Caltrans can be found at:
Other state and federal manuals and documents should be consulted for specific guidance in developing a project. Pertinent documents can be accessed through the Division of Local Assistance Home Page on the Internet at:
Back to Table of Contents
3.
DEFINITIONS
Table 3.1 provides the various definitions of key terms in regards to source inspection.
Term |
Quality Assurance |
Quality Control |
Independent Quality Assurance |
Verification |
23CFR637B |
All those planned and systematic actions necessary to provide confidence that a product or service will satisfy given requirements for quality. |
All contractor/vendor operational techniques and activities that are performed or conducted to fulfill the contract requirements. |
No definitions- typically referred as Oversight, which is defined as “Oversight is the act of ensuring that the federal-aid highway program is delivered in accordance with applicable laws, regulations and policies.” |
Sampling and testing performed to validate the quality of the product. |
Deputy Directive 90 |
The activities performed within the Implementing Agency during the project delivery process that provides confidence that the project team is fulfilling established project requirements and expectations. |
The operational processes, practices and activities performed at the project team level during the project delivery process to ensure that the product meets the project's purpose and need and fulfulls establishes quality requirements. |
The activities performed by the Department at a project level to ensure that the Implementing Agency’s quality assurance activities result in projects being developed in accordance with Department standards, policies and practices and the Quality Control plan provided by the Project Sponsor. |
No definitions |
Table 3.1: Definitions of Key Terms in regards source inspection
Table 3.2 is the glossary of commonly used abbreviations in the SIGLA manual.
Abbreviation |
Definition |
AAA |
Advertised, Awarded, and Administered |
AML |
Authorized Materials List |
CCO |
Contract Change Order |
CFR |
Code of Federal Regulations |
COC |
Certificate of Compliance |
CPD |
Caltrans' Construction Procedure Directive |
IA |
Implementing Agency |
IQA |
Independent Quality Assurance |
METS |
Materials Engineering and Testing Services |
NCR |
Non-conformance Report |
OSM |
Office of Structural Materials |
OSMR |
Oversight Structural Materials Representative |
QA |
Quality Assurance |
QAP |
Quality Assurance Program |
QC |
Quality Control |
QCP |
Quality Control Plans |
RE |
Resident Engineer (Local Agency Construction Team) |
RFI |
Request for Information |
SHS |
State Highway System |
SIGLA |
Source Inspection Guidelines for Local Agencies |
SIQMP |
Source Inspection Quality Management Plan |
SMR |
Structural Materials Representative |
SR |
Structure Representative (Local Agency Construction Team) |
Table 3.2: Glossary of Common Abbreviations
Back to Table of Contents
4.
RISK MANAGEMENT
The QA Acceptance Program includes an assessment of all materials based on importance. The appropriate level of source inspection is conducted based on this assessment. Materials with a higher consequence of failure such as main members and non-redundant members require source inspection 100% of the time while materials with less risk require less frequent inspection.
Level of importance may depend on:
- Consequence of failure (safety concerns)
- Monetary risk of failure
- Complexity of fabrication
- Specialty materials
- History of the material
- High maintenance cost
In order to manage the materials and source inspection for the project, the local agency’s quality assurance program should maintain a source inspection priority list. The list should include all main material components (bid items) as well as significant sub-components for the project. The list should be categorized based on the level of importance for their project which then corresponds to a source inspection priority.
Examples of materials with a higher source inspection priority that require source inspection 100% of the time are:
-
Structural steel bridge girders
-
Precast concrete bridge girders
-
Steel overhead sign structures
Less critical materials that may only require periodic source inspection are as follows:
4.1 Risk Assessment
Project Risk Management (PRM) is a process of planning for identifying, analyzing, communicating, managing, and responding to project risks through all phases of project delivery (see Figure 4.1). Risk management is a scalable approach that provides a level of effort that is appropriate to a particular project depending on its size and its complexity.
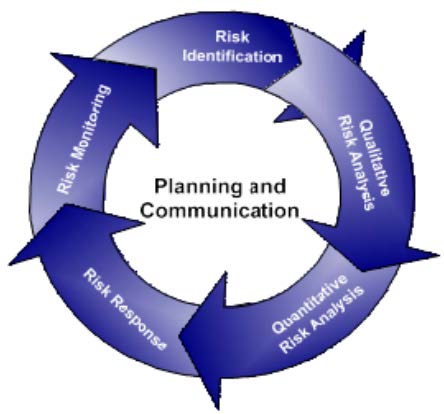
Figure 4.1 Risk Assessment Cycle
4.2 Project Material Risk Assessment Matrix
When developing the SIQMP, the Risk Assessment Matrix serves as a model to capture Project Risk Management related to source inspection. The Risk Assessment Matrix (see Figure 4.2) assists in performing a qualitative risk analysis in terms of probability and impact. When the form “Notice of Materials to be Used” is received and the Structural Material Representative (SMR) is required to determine resources for source inspection, the SMR can utilize the Risk Assessment Matrix to reevaluate previously determined high risk items requiring source inspection, and adjust resources as deemed necessary. The duties and responsibilities of the SMR are described in Section 5.1. Any updates to source inspection activities require an update to the SIQMP, which shall be submitted to Caltrans for review and approval. Refer to Section 6.2 for information regarding any deviations in performing source inspection for the structural material listed therein.
Risk = Probability x Impact
Probability indicates the chance of a material failing to meet the specification while impact indicates the consequences on a project if the material fails to meet this specification. Materials that rate for high in both categories (high risk of failing to meet specification and high risk of consequences if they do fail) should have the highest level of scrutiny by SMRs. The Risk Assessment Matrix assists in decision making for allocation of resources by answering the following questions:
-
What risks affect achieving project objectives?
-
Which are most important?
-
How do they affect cost and schedule?
-
What can be done?
-
How did the response affect change?
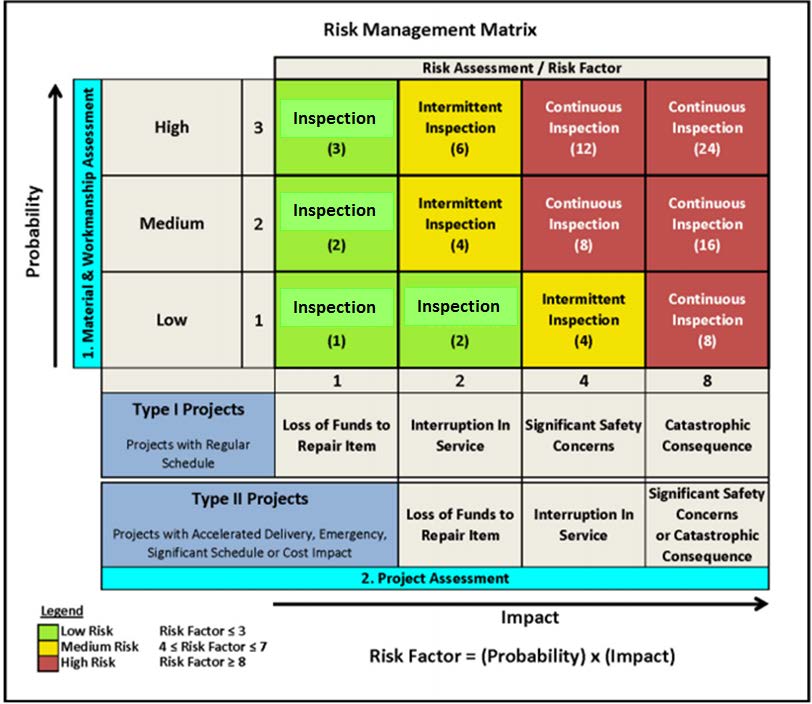
Figure 4.2 Risk Assessment Matrix
4.2.1 Probability: Measure of Material Failing to Meet Specification
Material and Workmanship Assessment: A fabricator’s standard of workmanship can directly affect the quality of the material fabricated. Because of such, in order to assess a product’s likelihood of not meeting specification, it is necessary for the SMR to have thorough knowledge of the fabricator’s history. Factors influencing a fabricators history include:
The assessment made by the Engineer should account for a facility’s ability to demonstrate adequate processes and resources to produce quality products. There are several components an Engineer needs to review in order to evaluate a facility’s workmanship history. The first step is evaluating the previous experience of working with that facility to gauge the frequency of past issues, types of issues, and likelihood of the issues’ recurrence.
Past performance can also be checked, items such as quality management issues, nonconformance involving the material being evaluated, and frequency of material production should all be evaluated. It is important to note that the number of issues or non-conformance reports (NCRs) at a fabricator may not accurately represent fabricators workmanship as a better representation is dependent on the volume of work has been done in the past. It is also important to account for the applicability of issues by assessing the issue details, the origin of the issue, and quality management involvement in resolving the issue.
From this assessment the SMR is to categorize a facilities workmanship on the Risk Assessment Matrix for that material as low, medium, or high probability of not meeting specification and obtain the corresponding Probability Value (1-3), see Figure 4.3.
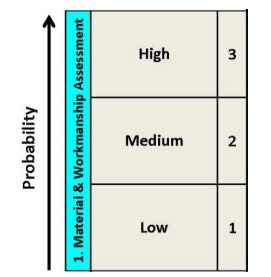
Figure 4.3 Probability Assessments (Y-Axis of Risk Assessment Matrix)
4.2.2 Impact: Consequences of Material Failing to Meet Specification
Project Assessment: Every project has risks, regardless of project size or complexity. Risks have negative or positive effects on at least one project objective (cost, time, scope, and quality). Two components used to perform a project assessment include: (1) evaluation of project type, and (2) evaluation of project impact due to material failure.
Project Type: Types of projects that SMR is typically involved with are:
-
Type I: Projects with regular schedule
-
Type II: Projects with accelerated delivery, emergency projects, or projects with significant schedule or cost impacts
Consequence of Failure: The second part of performing project assessments includes categorizing each product or material based on its highest consequence of failure. The highest consequence of failure is determined by the likely type of project impact a material failure would cause. Four types of project impacts are as follows:
-
Catastrophic Impact: Failure likely to cause loss of life or injury (e.g. strength properties, prestressing strand)
-
Safety Impact: Failure creates a safety hazard for employees or the public (e.g. reflectivity, pavement markers)
-
Interruption of Service: Failure or repair may cause an interruption in service (e.g. compaction, asphalt concrete)
-
Monetary Impact: Failure results in monetary loss only (e.g. galvanizing, steel irrigation pipe)
None of the project impacts are mutually exclusive and in turn, each progressive impact may include the consequences of lower impact; catastrophic impact being the highest concern and monetary impact being the lowest concern.
Once the project type and material consequence of failure are determined, the Engineer obtains the corresponding Impact Value (1-8), see Figure 4.4.
Figure 4.4 Impact Assessments (X-Axis of Risk Assessment Matrix)
Resultant Risk Assessment: Probability x Impact
The ultimate goal of the Risk Assessment Matrix is to assess risks associated with material fabrication and accordingly use optimum resources for source inspection. The Engineer is to determine a resultant Risk Factor (RF) as a product of Probability and Impact Values obtained from the respective assessments:
Risk Factor (RF) = Probability Value x Impact Value
Once the Risk Factor is determined, an appropriate level of source inspection is recommended using the Risk Assessment Matrix:
Risk Level |
Risk Assessment |
Resultant Risk Factor (RF) |
Recommended Action |
Low Risk |
Inspection at Jobsite |
RF ≤ 3 |
No inspection at the source. Materials insoection performed at the jobsite. |
Medium Risk |
Intermittent Source Inspection |
4 ≤ RF ≤ 7 |
Perform intermittent QA in-process inpsection at the source for fabrication. (e.g. anchor bolts, hoops, signal and lighting poles) |
High Risk |
Continuous Source Inspection |
RF ≥ 8 |
Perform continuous QA in-process inspection at the source for all fabrication activities (e.g. precast girders). |
Table 4.1 Risk levels
It is important to note that the evaluation of the resultant Risk Factor for a material can change throughout the life of the project as workmanship and project assessment are capable of shifting. At which point, the SMR is to re-evaluate and accordingly manage available resources.
Back to Table of Contents
5.
DUTIES AND RESPONSIBILITIES OF KEY PERSONNEL
5.1 Structural Material Representative
The Structural Material Representative (SMR) is a Transportation Engineer, Registered California Civil Engineer (PE).
Based on the project size and resource availability, the role of the SMR may be performed in conjunction with the Implementing Agency’s Construction Team such as the Structure Representative (SR) and/or Resident Engineer (RE) roles and responsibilities.
The SMR serves as the single point of contact between Fabricators and the RE/SR. The primary responsibilities of the SMR include:
- Providing input on the development (when possible) of the Source Inspection Quality Management Plan (SIQMP), which will be the guiding document for management of materials that are fabricated or produced outside of the jobsite
- Coordinating revisions to the SIQMP
- Performing Quality Control Plan (QCP) reviews
- Performing Shop Drawing reviews
- Performing Submittal reviews
- Peer reviewing Inspection Reports
- Serving as Implementing Agency point of contact on materials issues
- Participating in pre-fabrication meetings, pre-construction meeting, and pre-fabrication audits
- Meeting regularly with the RE/SR to establish and maintain open lines of communication throughout the life of the contract
- Providing clear, effective and timely structural materials recommendations to the SR/SR
- Anticipating and resolving any issues associated with quality assurance and source inspection while maintaining standards, consistency, contract schedule and contract cost
- Performing a Risk Assessment (RA) on all materials to determine if material requires source inspection
- Verifying fabrication facilities or materials are evaluated or pre-qualified for the project
- Performing fabrication facility audits, if deemed necessary
- Documenting when engineering judgment is used on an SMR Report or Material Suitability Documentation Report, Blue Tag. All SMR reports must be signed or co-signed by a registered engineer
- Verifying that all issues and non-conformances are resolved before material is tagged and shipped to the jobsite
- Providing clear, effective and timely structural materials recommendations to clients
5.2 Quality Assurance Inspectors
Inspection personnel perform technical assignments to either the field or the office. However, most inspectors are assigned to field duty (facility visits/source inspections). Field duties include performing inspections and documenting the results in the required reports. Inspectors must be an employee of the Implementing Agency or must be hired by an Implementing Agency subcontractor providing only QA services. The Inspector must not be employed or compensated by the Contractor or any of their subcontractors. Inspectors assigned to the office are typically at the Associate Inspector Level.
The responsibilities of the Inspector include at a minimum:
-
Verifying required documentation is provided, such as Certificate Of Compliance (COC), Mill Certs, Test Results, etc. at the time of inspection and release of product
-
Verifying Buy America requirements are met
-
Performing in-process inspections, verify QC processes and procedures are followed as outlined in QCP
-
Writing inspection reports
-
Issuing non-conformances on products or QC processes
-
Assisting SMR in QCP reviews
-
Assisting SMR in Shop Drawing reviews
-
Assisting SMR in Submittal reviews
Types of reports generated by Implementing Agency Inspectors include:
- Quality Assurance Nonconformance Report
- Report of Inspection of Materials
- Notice of Shipment of Material
- Material Suitability Documentation Report
- Material Suitability Report
- Welding Inspection Report
- Welding Witness Report
- Concrete Inspection Report
- Source Inspection Report
-
Paint Inspection Report
Type of release tags used for releasing fabricated materials by Implementing Agency Inspectors:
-
Orange Tags:
-
Inspected material conforms to contract documents
-
Material no longer requires source inspection
-
Responsibility for material is transferred to the RE
-
Green Tags:
-
Material transferred from one vendor to another vendor
-
SMR/Inspector still responsible for inspection
-
Should not arrive at the jobsite
-
Blue Tags:
-
Material that does not fully conform to contract document
-
Engineering analysis that determines material is suitable for intended purpose
-
Requires concurrence from the design team, the RE, and SMR
Implementing Agency Inspectors shall meet the minimum certifications per 2010 Standard Specification and SIQMP Outline:
Back to Table of Contents
6.
GENERAL INSPECTION INSTRUCTIONS
6.1 General
The Implementing Agency’s Source Inspection staff (SMR staff) is responsible for inspection, sampling and testing of structural materials and products for compliance with contract requirements to be used during construction.
In order to avoid impacting a project’s construction schedule, the SMR staff is required to understand internal procedures as outlined in this section, in order to streamline the material inspection and release processes.
6.2 Quality Assurance of Structural Materials Bid Items
The agency implementing the construction contract (Implementing Agency) on the State Highway System (SHS) is responsible for acceptance of the materials and workmanship, and it cannot be assigned to the contractor or to a consultant working for the contractor, regardless of the project delivery method.
One of the largest factors in transportation planning is the need to ensure that all systems, regardless of size or scope, are safe and efficient for the traveling public. The California Department of Transportation takes these responsibilities seriously, as evident by its goals to provide the safest transportation system for workers and users, and to effectively deliver quality projects, products and services. OSM METS (Office of Structural Materials - Materials Engineering and Testing Services) has developed a list of items to provide practices, procedures, and guidelines to assure the quality of materials and construction in all Federal-aid highway projects on the National Highway System. At a minimum, the Implementing Agency shall perform source inspection of the following material prior to release to the jobsite:
-
Precast prestressed concrete girder
-
Precast prestressed concrete deck unit (slab type)
-
Precast prestressed concrete slab
-
Prestressing strand
-
Precast jointed concrete pavement
-
Individual precast slab replacement
-
Precast concrete box culverts
-
Structural steel (bridge)
-
Structural steel
-
Painted structural steel
-
PTFE spherical bearings
-
Column casing
-
Sign Structure
-
Headed bar reinforcement
-
Furnish steel piling (Class N)
-
Ground anchors and soil nails
-
Miscellaneous metal (restrainer - cable type)
-
Reinforced concrete pipe (60” or greater)
-
Structural Steel for building work
- Mechanically Stabilized Earth (MSE) panels
-
Anchor bolt assemblies
-
Resistant-butt-welded hoops
- Electrical components
-
Epoxy coated reinforcing bar
Items which require further inspection and testing at the jobsite by the Implementing Agency include:
-
Field welding
-
Mechanically coupled reinforcement bar
If the Implementing Agency decides to deviate and not perform source inspection on any of the items listed above, a risk assessment analysis is required to be provided and approved by Caltrans prior to fabrication. A form provided in Appendix 7 is required to be filled out and submitted to METS for review and approval. After Caltrans METS responds with the affirmative to the agency's request for deviation, the Implementing Agency can move forward with implementing the change.
6.3 Materials Meeting
At the beginning of every job, the SMR is to coordinate a materials meeting with the Implementing Agency's designated RE and SR. It is beneficial to invite the Contractor to the meeting as the information discussed can help streamline processes and keep all parties aligned.
The SMR is expected to be knowledgeable in the fabrication and source inspection processes, and explain how these activities will meet the requirements of the SIQMP and project documents. The SMR discusses material requirements unique to the contract, potential source inspection issues, and the reporting and distribution system. The SMR emphasizes the need for timely submission of "XX-3103 Notice of Materials to be Used". When discussing the reporting system, the SMR clearly explains the purpose of non-conformance reports (NCRs) and the importance of timely, properly documented resolutions.
The SMR discusses the procedures to support the RE/SR, including a general approach to how SMR receives contract documents such as: addenda, design drawings, shop drawings, quality control plans, submittals, Requests for Information (RFI), and any other contract correspondence which affects source inspection or clarifies contract requirements. The SMR also explains materials release procedures and NCR notification procedures and protocol.
At the materials meeting, the SMR:
-
Discusses any materials concerns the RE and SR may have
-
Provides a list of materials requiring a “XX-3101 Notice of Materials to be Used”
-
If applicable, discusses with RE and SR that pre-weld and/or pre-precast meetings shall be held. Actual scheduling of the meetings can be finalized at a later point once Contractor is contacted and the fabricator is known
-
Determines a general approach to inform SMR of contract addendums, change orders, pertinent contract correspondence, and shop drawings
-
Determines if the pre-construction meeting with the Contractor has occurred and requests to be included
-
Provides a list of material-related submittals that must be received and reviewed by SMR
-
Discusses appropriate construction meetings in which the SMR’s participation would benefit the contract
6.4 Buy America
“Buy America” applies to all federal-aid contracts. “Buy America” requirements also apply to all contracts within the scope of a National Environmental Policy Act (NEPA) determination, regardless of whether the contract uses federal funding.
In order for a manufactured product to be considered subject to “Buy America”, the product must be manufactured predominantly of steel or iron and meet the following criteria:
Above requirement applies to steel or iron delivered to the job site for installation and where any precast concrete products are manufactured.
Under this law, steel and iron materials must be melted and manufactured in the United States except:
-
Foreign pig iron and processed, pelletized, and reduced iron ore may be used in the domestic production of the steel and iron materials
-
If the total combined cost of the materials does not exceed the greater of 0.1 percent of the total bid or $2,500, materials produced outside the United States may be used if authorized.
All melting and manufacturing processes for these materials, including an application of a coating, must occur in the United States. Coating includes all processes that protect or enhance the value of the material to which the coating is applied.
For steel and iron materials to be incorporated into the work, certificates of compliance (COC) and certified mill test reports shall be furnished. Mill test reports must indicate where the steel and iron were melted and manufactured and this information is verified by Quality Assurance inspector.
Below are examples of Buy America compliance that steel mills can put on their Mill Test Reports:
- “All melting and manufacturing processes for the product occurred in US”
- “100% melted and manufactured in the USA”
The minimum allowance for the use of small quantities of foreign steel may be approved by the RE.The Inspector does not have authority to make such an approval.
When foreign steel is released, note on the Report of Inspection the items that are foreign steel with an additional note that this has been approved by the RE. The Implementing Agency Inspector may be the only owner's representative to verify conformance to "Buy America" requirements. Therefore, this verification is mandatory.
6.5 Quality Assurance Non-Conformances
Non-conformance reports (NCRs) are an integral component of inspection process. The purpose of the NCR is to document material or workmanship that does not meet the contract requirements, or breakdowns in the QC process. They are utilized to communicate to the Implementing Agency's Resident Engineer when SMR staff discovers non-compliances with contract specifications. When situations arise that do not meet all applicable contract requirements, the inspector/SMR initiates the non-conformance process using the "Quality Assurance - Non-Conformance Report". The complete process is outlined in Section 11 of this manual.
6.6 Substituted Materials
When specific brand or trade names are used to designate required products, the Brand or Trade Names and Substitutions contractor may furnish other products that are of equal or better quality. A product is not necessarily equivalent merely because it is on an approved products list. These lists indicate that the products meet the general qualifications. However, some of the listed products may not meet the specific needs of the project or may not be appropriate for a particular location due to factors such as climate conditions or maintenance difficulties.
For substituted materials, Request for Information (RFI) or Contract Change Order (CCO) is required to be accepted for the job. Any deviation from special provisions must have approval from the RE.
SMR needs to investigate and determine whether material substitution is suitable to be used on the project. Such materials might require further testing in addition to specification requirements to be considered suitable for use for the application intended. Document when engineering judgment is used on an SMR Report or Material Suitability Documentation Report, Blue Tag.
6.7 Certification of Compliance
Section 6-2.03C “Certificate of Compliance” of the Standard Specifications, specifies the requirements and uses of Certificates of Compliance (COC). The approved quality control plan required for some products may additionally require that a Certificate of Compliance be supplied.
When the “Buy America Act” applies (see SIGLA Manual Section 6.4 “Buy America” & Construction Manual Section 3-604 "Buy America Requirements") to steel products, the manufacturer must supply a COC stating that all melting and manufacturing processes used to produce the material have been performed in the U.S.A.
This certification must also satisfy any additional requirements of the contract’s special provisions. An authorized representative of the producer, typically the quality control manager, must sign the COC.
The Implementing Agency Resident Engineer (RE) can accept certain materials without sampling and testing, if accompanied by a Certificate of Compliance (COC), acceptable on from those sources that have prior records of proven reliability and established quality control.
The RE may also reject the material even with a COC if quality assurance testing has resulted in failing tests or the supplier has failed to perform satisfactory quality control practices. Standard Specifications identify materials requiring a Certificate of Compliance. Typical items include:
-
Portland cement
-
Elastomeric bearing pads (plain and steel-reinforced)
-
Reinforcing bars
-
Chemical adhesives for structures
-
Concrete admixtures
-
Concrete curing compound
-
Chain link fencing and railing
-
Anchorage devices
-
Cable-type restrainers
Refer to Section 6-203C of the Construction Manual “Materials Accepted on the Basis of a Certificate of Compliance" for a list of items accepted at the jobsite on the basis of a COC.
It should also be noted that when a material is on the Authorized Material List (AML), it does not waive COC requirements specified in contract documents.
Back to Table of Contents
7.
SOURCE INSPECTION PROCESS FLOWCHARTS
Figure 7.1 provides the general Caltrans oversight process with Local Agencies.
Figure 7.1 Caltrans Oversight Process with Local Agencies
Figure 7.2 provides the general Caltrans - METS Source Inspection process as an example.
Figure 7.2 Source Inspection Process
Figure 7.3 provides the Source Inspection Process Deviation Protocol.
Figure 7.3 Source Inspection Process Deviation Protocol
Back to Table of Contents
8.
CONTROL OF DOCUMENTS
It is the responsibility of the Implementing Agency to develop a system for Control of Documents and Records. The purpose of the Document and Record Control System is to ensure only the most recent revisions of controlled documents and records are available to appropriate personnel, and revisions are timely and have received all required approvals. Additionally, archiving and retrieval of documents and records have to be included in this system.
8.1 Scope
Establish a document and record control systems that identifies, stores, and manages documents and records related to implementation, maintenance of Source Inspection Quality Management Plan (SIQMP). Specially:
- All documents and records are reviewed and approved by designated personnel prior to issue for use
- Document changes are approved by designated personnel and reasons for change are documented
- A master list of all documents, indicating current authorized versions, is maintained
- Pertinent current issues of documents are available at all locations where operations essential to the effective functioning of the quality system are performed
- Changes and the current revision status of the documents are identified
- Invalid and/or obsolete documents are promptly removed to prevent the unintended use and to apply suitable identification if they are retained for any purpose
- Documents are legible and are readily identifiable
- Any obsolete documents retained for legal or knowledge/preservation purposes are suitably identified
- Documents of external origin necessary for planning and operation of the Local Agency are identified and their distribution controlled
- Quality documents and records are identified, archived, and retrieved in a defined and acceptable manner
Back to Table of Contents
9.
FORMS
The Implementing Agency is responsible for developing a Quality Assurance Program (QAP) to assure that the materials and workmanship incorporated into each construction project are in conformance with the requirements of the approved plans and specifications, including approved changes. The program must meet the Title 23, Code of Federal Regulations, Part 637 (23 CFR 637) requirements. Part of this program necessitates the implementing agency to develop standard forms to be used during source inspection activities. Caltrans has developed an extensive library of standard forms to meet this requirement. An implementing agency may derive their forms from our standard library and alter them as seen fit. For ease of communication across agencies, the local agency is required to keep the Caltrans form number, buy alter the prefix, header, footer, and any references to Caltrans, METS, OSM, etc. For example, Caltrans has developed a notice of materials to be used for, “CEM-3101”. The local agency needs to use the same form number “3101” but replace “CEM” with an acronym of their choosing. Examples of widely used OSM Forms are located in the Appendix 8.
Back to Table of Contents
10.
MATERIAL SAMPLING AND TESTING
10.1. Tagging and Sampling Procedures
In some cases, material is required to be sampled and tested prior to tagging and releasing. A Sample Identification card, or XX-101, is the form used for a sample that is being sent to the testing facility that the Implementing Agency has previously designated. The XX-101 is used to document material information for the testing lab to ensure traceability of the material being sampled. The implementing Agency should ensure there is a process in place for the testing facility to notify the Agency when test results are complete. The Implementing Agency should ensure that test results are logged and made easily available. Figure 10.1 provides the tagging and sampling procedure as an example.
Figure 10.1 Tagging and Sampling Procedure
10.1.1 Proper Sampling
Verify that the SIQMP sampling procedures and numbers comply with the project’s special provisions for information about specialized items that require a particular type or number of samples.
-
Correct number of samples for required testing – The number of samples are based on project specifications, Caltrans Standard Specifications, ASTM, AASHTO, and ANSI requirements. Verify that QC results meet the specification requirements - Manufacturer’s QC data must show compliance with specifications. They must be legible and understandable. The testing data must support the included Certificate of Compliance.
-
Size and type of sample - Some materials require specific lengths and configurations. Steel plate or bar size maybe controlled. Sample may have to come from within the component. For example: See Standard Specification Section 51-1.12H(2) Steel Reinforced Elastomeric bearing pads 2” or thicker.
-
Sampling must be performed by the RE or a designee on his behalf. Sampling cannot be performed by any Quality Control function including but not limited to fabricators and contractors.
Please see Appendix 9 for table of material sampling frequencies and testing requirements. This table is not all inclusive but is meant as general guidance to some items requiring sampling and testing.
10.1.2 Documentation Guidelines
10.1.2.1 Sample Identification Card
A Sample Identification Card, form XX-101 must accompany samples for QA testing at the designated testing facility. Documenting the right information on the XX-101 form, obtaining and verifying the relevant backup documentation makes the testing process much more efficient. These forms can be filled out manually or electronically. Samples must be properly identified so the testing facility can function efficiently and report the results in a timely manner to the project.
- Materials test reports - Final product test results should be in readable format. Should include which tests were done to which specifications.
- Mill test reports – Parent (source) materials analysis and physical test results from the metal foundry must be included with many products. These suppliers must meet ASTM specification requirements and should comply with Buy America requirements (see SIGLA Section 6.4)
- Tracking numbers from supplier - Product must be identified by some combination of the following: lot #, heat #, load #, or release #. All must be traceable back to the parent material mill test reports and certificates of compliance.
- Project information - Contract information is a must; Resident Engineer, Structures Representative, expense authorization (E.A.) or project number, the name of the person who took samples or witnessed the sampling process.
- Because each specification year may have different requirements, verify the applicable specification year (example: Caltrans 2010).
- Identify the material on the form by its specification name rather than by its trade name completely fill out Sample Identification cards.
Sample traceability – To have proper traceability all documents must match and the reference numbers must be carried over from one document to another. Without traceability the samples should not be tested. Detailed instructions for filling out Sample Identification Cards as well as a completed form are located in Appendix 10.
10.1.3 Handling of Samples
Packages containing samples may be damaged on their way to the testing facility. This damage may separate documentation from the sample or obscure the sample identification if it is not marked and secured properly. To ensure proper identification of samples the following requirements must be met:
-
Packaging - Wire tie or strapped together, box or bag, shrink wrapped or taped.
-
Proper & secure identification - XX-101 should be with sample. Painted on identification or wired on tags. Clear tape over printed labels.
-
Protection from weather - Identification labels and XX-101’s must be protected from moisture and damage.
-
Coating protection - Coated samples should be encased in some protecting medium such as foam pipe insulation for epoxy coated rebar.
-
Timely shipping or delivery is essential – Do not hold the samples for a group shipment. Ensure that samples are shipped within a few days.
10.2 Testing
10.2.1 Laboratory Requirements
A verification sampling and testing program must be established by the implementing agency. In order to avoid an appearance of a conflict of interest, any qualified private laboratory shall perform only one of the following types of testing on the same project: Verification testing, QC testing, or dispute resolution testing. Each project specific SIQMP, with respect to the laboratory, must describe the following:
- Verification of lab qualifications for the applicable materials on this project (e.g. ISO 17025 for steel, and AASHTO Accreditation Program (AAP) for concrete).
- Provide a list of verification tests to be performed by the implementing agency along with the frequency and applicable industry standards to be used/specified (ASTM, CTM, etc.). A template for the list is provided in Appendix 11.
- Describe the verification materials testing filing system and the physical location it may be reviewed during audits.
- Test results for material samples must be documented.
- Provide example forms that will be used for sampling material and reporting test results.
- Provide a statement that there are no conflicts of interest regarding the verification lab and any other acceptance activities for the project.
Back to Table of Contents
11.
NONCONFORMING MATERIALS
11. Nonconforming Materials
11.1 Quality Assurance Non-Conformances
Non-conformance reports (NCRs) are an integral component of the Quality Assurance (QA) inspection process. The purpose of the NCR is to document material or workmanship that does not meet the contract requirements, or breakdowns in the Quality Control (QC) process. They are utilized to communicate to the designated Resident Engineer (RE) when QA personnel discover non-compliances. When situations arise that do not meet all applicable contract requirements, QA personnel initiate the nonconformance process using the Form XX-15, “Quality Assurance - Nonconformance Report”.
The RE has the responsibility to make the final decision regarding the incorporation of the material into the project.
Example situations requiring an NCR:
- QA Inspector identifies material/workmanship that does not meet contract requirements, and the deficiency is not corrected within that work shift.
- The third occurrence of the same deficiency regardless of the contractor’s ability to correct the problem within a work shift. The NCR would detail the QC’s inability to address root causes of the issue.
- Any systemic nonconformance regardless of the contractor’s ability to correct the problem within a work shift.
- Any action taken by QC that is not in conformance with the contract requirements or any attempts to hide nonconforming processes or products.
- Material is shipped without proper inspection and release documentation.
Example situations NOT requiring an NCR:
- Material that has not yet been inspected or accepted by the contractor’s QC personnel.
- First or second occurrence of a deficiency if QC personnel acknowledge the problem and ensure that it will be corrected within that work shift.
- Nonconformance that has been identified by QC and will be repaired during production unless it is a systemic nonconformance or a third occurrence of the same deficiency as mentioned above.
If any clarification is needed regarding issuance of an NCR the SMR will discuss the issue with the appropriate personnel in the Implementing Agency’s chain of communication. The oversight SMR (OSMR) may also be contacted for guidance. Once determined that an NCR should be written, the SMR is responsible for notifying the RE as soon as practically possible, preferably in person or by phone.
Procedure to issue an NCR:
-
After QA locates a problem or deficiency, QC and/or a responsible representative from the contractor needs to be promptly informed of the finding. QA inspectors will identify to the contractor areas of nonconformance; however, written NCRs will not be provided to the contractor or quality control personnel.
-
The QA inspector should NOT stop the work under any circumstances unless specifically authorized by Resident Engineer.
-
The inspector contacts the project SMR to discuss the issue as to whether an NCR is required.
-
SMR gives verbal notification to the Resident Engineer (RE) or Structures Representative (SR) as soon as practically possible.
-
Inspector drafts the NCR including any relevant conversations with contractor or QC personnel in the report. The QA inspector then submits the draft NCR to the SMR for review.
-
The SMR reviews the NCR for accuracy and transmits the NCR to the RE and/or SR within 24 hours of the determination that a nonconformance report needs to be written.
-
A copy of the NCR is transmitted to the Oversight SMR for informational purposes only.
-
An illustration of both the verbal notification and written notification process of NCRs are shown in the Figures 11.1 and 11.2.
Initial Verbal Notification of NCRs
Process should be complete as soon as practically possible.
Figure 11.1 Flowchart for verbal notification of NCRs.
Written Notification of NCRs (XX-15)
Process should be complete within 1 Working Day of NCR.
Figure 11.2 Flowchart for written notification of NCRs.
An inspector or SMR will complete a XX-16, “Quality Assurance Nonconformance Resolution”, when the proposed resolution is submitted by the Contractor and SMR, RE and SR are in agreement with the proposed resolution. The SMR will track the number of outstanding NCRs and work with the Resident Engineers and Structure Reps to reach a resolution. SMRs are responsible for acquiring signed correspondence from the RE or SR. If the SMR and RE or SR reached a resolution during a telephone conversation, the SMR will attempt to get a response in an e-mail documenting the conversation.
11.2 Material Suitability Release
11.2.1 Determination of Suitability
Material suitability release procedures may be developed as a mechanism to keep projects moving forward, better document material suitability decisions, and to ensure proactive resolution of material issues. The Inspector is not authorized to release material if it does not conform to the specifications, contract plans, and approved working drawings without proper authorization. However, the material suitability release procedures allow QA staff to release material if an engineering analysis has determined the material will be suitable for its intended purpose. The purpose of this section is to provide guidelines for procedures to execute this system.
The Material Suitability Release Procedures Process
The alternative release procedures shown in Figure 11.3 will allow inspectors to release material when the SMR has determined that it is suitable for its intended purpose in the project. This material suitability process may be initiated by one of the following:
-
A Nonconformance Report (NCR)
-
Contractor Requests Information (RFI)
-
Meeting, Submittal, SMR Observation, Other
After one of these instances occurs, the Inspector and SMR should discuss the issue and come to consensus whether a nonconformance or change to the contract has occurred.
Once consensus is reached between the Inspector and SMR, the SMR will contact the Resident Engineer (RE) and/or Structure Representative (SR) in order to notify them of the deviation to the contract. Additionally, the SMR will inform the Contractor of the issue in order to initiate discussions and develop possible resolutions. During this time, it will be important for the SMR to sufficiently research the issue in order to facilitate the best materials engineering technical recommendation. The SMR will also prepare a memorandum to the Implementing Agency’s Construction Team in order to aide in issuing official correspondence notifying the Contractor of the issue and request a proposal to resolve the issue. Once the Contractor has responded to the official correspondence, the SMR should proceed with one of the following courses of action:
1. Acceptance Proposal from the Contractor
If the Contractor proposes a resolution that the SMR, Construction Team and Designer can agree to, the SMR will document the issues and decisions on the appropriate forms (9) and forward to appropriate personnel in the chain of communication for review. Upon approval, the SMR will verbally notify the Contractor of the Implementing Agency’s approval of the resolution.
2. Unacceptable Proposals from the Contractor
If the Contractor proposes a resolution that the SMR, Construction Team and Designer do not agree with, the SMR will record the issue and resolution on the appropriate forms (see Section 9) and will verbally notify the Contractor of the Implementing Agency’s rejection of the resolution.
3. Proposals from the Contractor Without Project Team Consensus
During the course of a project there may be instances where the Construction Team or Design Team does not agree with the technical recommendation issued by the SMR. If the SMR, RE/SR, and the Design Team cannot gain consensus on how to best move forward with the material, the project team will escalate the issue to the appropriate personnel in the chain of communication who will be the final decision making authority for materials and fabrication issues on the project.
4. Materials Brought Back into Conformance
If the Contractor proposes a solution that will bring the material back into conformance with the Contract, the SMR will record the resolution on the appropriate forms and may authorize release under form XX-29 (Appendix 8).
Projects with material released to the jobsite under the material suitability release process may require Contract Change Orders (CCOs). The SMR may assist with review of CCO language for technical accuracy before it is forwarded to the Contractor.
Figure 11.3 Alternative Release Procedures - Material Suitability Process
11.2.2 Documentation of material suitability and release
Sample XX-6013 – “Material Suitability Documentation Report”
The SMR will complete the XX-6013 in order to provide a summary of the issue and documentation of the decisions made by the SMR, the Construction Team, and Design. One XX-6013 should be completed for each issue that can potentially result in a material suitability release. The XX-6013 should be treated as a working document that is updated daily and summarizes all of the ongoing discussions and decisions regarding a material issue. The SMR will be ultimately responsible for completing and updating this report as the resolution of the issue changes and decisions are made by the appropriate parties. A blank copy of the XX-6013 is located in Appendix 8.
Sample XX-6014 – “Material Suitability Report”
For nonconforming material that has been found fit for its intended purpose, the Inspector will complete the XX-6014 to replace the XX-29 or modify the XX-6011 that would typically be completed for conforming material. See Appendix 8 for blank XX-6014 Material Suitability Report form.
The following guidelines shall be followed when determining the type of Blue Tag for material release:
-
Material shall be released with a XX-6014 if the material has been evaluated and determined to be suitable for its intended purpose and it or its parent material no longer requires in-process inspection.
-
Material shall be released using a Green Tag Report (XX-###) with a note describing the material suitability issue if the material is evaluated and deemed suitable for its intended purpose and is being shipped from one vendor to another vendor where the Local Agency is still responsible for inspection (i.e. strand or rebar going to a pre-cast yard). This is important as another inspector will need to be aware of the material’s deficiency with the contract specifications. Note: A modified Green Tag Report (XX-###) may have a note on the tag identifying the material as having been evaluated for suitability, or some other modification, such as a sticker.
Back to Table of Contents
12.
QUALITY CONTROL PLANS
This section discusses Quality Control Plans (QCP) that are required for material that will be source inspected and therefore the review, approval, and implementation must be addressed in the Local Agency’s SIQMP. QCPs for items not requiring source inspection will still require review and approval by the RE (i.e. HMA QCP when applicable), but are not part of the scope of this document or the SIQMP.
12.1 General
A QCP details the methods the contractor will use to ensure the quality of the work. QCPs must meet or exceeded the material, testing and inspection requirements specified in the project contract documents. The project contract documents will specify if a pre-job meeting is required to discuss a quality control plans. Local Agencies are required to discuss all QCP that are applicable to their project in their SIQMP as discussed in Section 2.4 of the SIQMP Outline.
12.2 Typical Quality Control Plans
Below are some of the typical QCPs that are most likely to be required per the project contract documents. The Local Agency is responsible for identifying all QCPs required by the project contract documents in their SIQMP.
12.2.1 Splice Prequalification Quality Control Plan (SPQCP)
12.2.1.1 SPQCP for Mechanical Couplers and Resistance-Butt-Welded Splices (Hoops)
Mechanical couplers are a method used to splice rebar together. Resistance-butt-welded splices are commonly referred to as hoops because the rebar is formed in a circle and then machine resistance-butt-welds the ends together forming the shape of a hoop. The type and model of mechanical couplers and the fabricators of hoops are both required to be on the Authorized Material List. See Section 14 of this manual for more information on Authorized Material Lists. The fact that the couplers and hoop manufacturers are on the Authorized Material List does not exempt them from submitting a SPQCP.
Per Section 52-6.01C(4) of the 2010 Standard Specifications, a splice prequalification report is required to be submitted and approved before production can begin on hoops or couplers.
Per Section 52-6.01C(6)(b) of the 2015 Standard Specifications, welder and welding procedure qualifications are required to be submitted as an informational submittal for hoops.
Per Section 52-6.01C(6)(c) of the 2015 Standard Specifications, a splice prequalification report is required to be submitted and approved before production can begin on couplers.
Note that hoops are exempted in the 2010 and 2015 Standard Specifications from requiring a Welding Quality Control plan described below.
12.2.1.2 SPQCP for Headed Bar Reinforcement
Per Section 52-5.01C(1) of the 2010 and 2015 Standard Specifications, “If any part of the head is fabricated in the field, submit a prequalification report as specified for service splices and ultimate butt splices under section 52-6.01C(4).”
12.2.2 Precast Concrete Quality Control Plan (PCQCP)
Section 90-4 of the 2010 Revised Standard Specifications and Section 90-4 of the 2015 Standard Specifications provides minimum requirements for inspection and testing of precast concrete members. Section 90-4 also stipulates different “Tiers” of precast items. Precast members listed as Tier 1 or Tier 2 require a PCQCP and have more stringent QC requirements than Tier 3 or Tier 4 precast members. The PCQCP must be job specific and comply with all contract requirements.
12.2.3 Welding Quality Control Plan (WQCP)
Section 11-3 of the 2010 Standard Specification and Section 11-2 of the 2015 Standard Specification specifies when a WQCP is required. Note that Section 52-5 and 52-6 of the 2010 and 2015 Standard Specifications exempts hoops and headed bars from requiring a Welding Quality Control Plan.
A Local Agency can adopt these requirements. Any modifications to these requirements should be clearly identified in the SIQMP.
12.2.4 Non-Project Specific Welding Quality Control Plans
OSM has preapproved some WQCPs at audited facilities that are valid as long as the facility is on the audited facility list and are only valid for shop welding (not valid for field welding). If a facility is on an OSM audited facilities list, then their shop WQCP is not required to be submitted on a project by project basis. The facility is still required to submit shop drawings and any other submittal required in the contract documents before they begin fabrication. See Section 14 for more information about the Audited Facility List.
The Local Agency may choose to adopt the OSM audited facilities list and the preapproved WQCP or may develop its own audited facilities list and approve WQCPs on a job specific basis.
During source inspection, QA inspectors must ensure that fabrication complies with all contract requirements including the facility WQCP. The following types of facilities on the OSM audited facility list have shop approved WQCPs that are not required to be submitted and approved before they begin fabrication:
- Welded Steel for Overhead Sign Structures
- Welded Steel for Signal and Lighting Pole Structures
- Steel Pipe Piling
12.2.5 Other Quality Control Plans
Less frequent QCPs may be required in the contract documents. The Local Agency is responsible for identifying all QCPs in their SIQMP.
12.3 Review Guidance
All QCPs must be submitted through the prime contractor to the RE. The RE may forward the QCP to the SMR for comments as needed. An appropriate review form shown in Appendix 8 of this manual is required for each submittal. All review forms must be kept in an appropriate filing location and in general compliance with Caltrans Construction filing requirements. The Local Agency is responsible for generating a detailed procedure for the review process of QCPs. See Section 2.4 of the SIQMP Outline for more details.
Back to Table of Contents
13.
SHOP PLANS AND DRAWINGS
Shop drawings are required for material as specified in the contract documents. Local Agencies are required to include a list of all materials requiring shop drawings for their project as well as a documented review process in the SIQMP outline.
13.1 Review Guidance
All shop drawings must be submitted through the prime contractor to the Implementing Agency’s designated Resident Engineer (RE). The RE may forward the shop drawings to the SMR for comments as needed. An appropriate review form as mentioned in Section 9 of this manual is required for each submittal. An example shop drawing review form is provided in Appendix 8. All review forms must be kept in an appropriate filing location and in general compliance with Caltrans Construction filing requirements. The Local Agency is responsible for generating a detailed procedure for the review process of shop drawings.
Back to Table of Contents
14.
AUTHORIZED MATERIALS LIST AND AUDITED FACILITIES LISTS
METS has developed and is responsible for developing and maintaining multiple approved products lists and audited facility lists. There are many references in the Standard Specifications that require material or facilities to be on these lists.
If a Local Agency requires Caltrans Standard Specifications to be part of the project documents, they have two options described in Sections 14.1 and 14.2 to meet its requirements.
14.1 Adopting METS Authorized Materials Lists and Audited Facilities Lists
The Local Agency can adopt all or some of the Authorized Materials Lists and Audited Facilities Lists developed and maintained by METS. The Local Agency assumes all responsibility for material coming from these facilities. Just because material is on the Authorized Materials List or is fabricated at an Audited Facility does not guarantee that it will comply with the project contract documents, nor does it exempt the Local Agency from performing the level of QA inspection and testing required to ensure a quality product. Also note that for Caltrans implemented projects, additional QA processes are employed at these facilities in order to accept source inspected materials.
14.2 Develop Local Agency Authorized Materials Lists and Audited Facilities Lists
The Local Agency can develop some or all of its own Authorized Materials Lists and Audited Facilities Lists. These lists can be project specific or developed and maintained for all projects within the jurisdiction of the Local Agency. Any list (even if only one product is on the list) must be submitted along with all applicable test data, reports, and documentation to Caltrans METS for approval before it can be referenced in the project’s SIQMP. Contact the OSMR for additional information.
Back to Table of Contents
15.
SIQMP REVIEW AND APPROVAL
When the Local Agency enters into a cooperative agreement with Caltrans, the Local Agency is required to submit a Source Inspection Quality Management Program (SIQMP) to the State Materials Engineer via the Oversight Structural Materials Representative, for review and approval. Approval of the SIQMP is required prior to Caltrans’ issuance of the project’s encroachment permit.
Local Agencies are required to develop an SIQMP in accordance with the direction outlined in Appendix 5. They are also required to use the same paragraph numbering system and must include all sections listed in the outline. The Local Agency can reference sample SIQMPs in Appendix 6.
The respective district OSMR is available at the onset of every local agency project to answer any questions on putting together the SIQMP document.
15.1 Revisions vs. Addendums/Amendments
Prior to receiving approval to the SIQMP, submit any corrections based on METS’ review comments as “Revisions.” A revision to the SIQMP is a submittal which contains the entirety of the contents required as defined by the SIQMP Outline. Once the SIQMP has been approved for use on the project, submit only the updates (lab certifications, personnel certifications, additional processes/procedures, etc.) as addendums or amendments.
15.2 METS’ Review Timeframe
Provide METS a minimum of 10 working days for a review.
When METS provides comments back to the Local Agency to address, the Local Agency will receive a letter and a review form indicating which portions of the SIQMP require corrections.
15.3 SIQMP Noncompliance Letter
If METS and the Local Agency cannot come to an understanding within the allotted timeframe, the OSMR will issue an SIQMP noncompliance Letter. This letter will list a summary of the review findings and any deficiencies with the submittal.
15.4 Appeals Process
In the event an Local Agency and the OSMR cannot come to an understanding regarding the effectiveness of the Local Agency’s quality assurance procedures, the Local Agency can request reconsideration of the OSMR’s position by the Federal Acceptance, Review, and Evaluation (FARE) consisting of the Chief of the Office of Structural Materials, the Chief of the Office of Roadway Testing, and the Area Construction Manager. Requests for consideration shall be submitted in writing to the FARE panel with a complete description of how the Local Agency’s quality assurance procedures ensure project components comply with Caltrans policies, standards, procedures, and best practices.
Requests should be marked to the addition of the FARE panel and sent to the following address:
Material Administrator Mail Station #5
Materials Engineering & Testing Services
5900 Folsom Blvd, Sacramento, CA 95819
Fax: (916) 227-7084
materialsadministratormets@dot.ca.gov
The FARE panel will review and respond to requests within 10 working days.
15.5 METS’ Approval
Once the Local Agency’s SIQMP adequately addresses the project’s source inspection needs, METS will issue a SIQMP Approval Letter to the Local Agency. A sample approval letter is attached in Appendix 12.
15.6 SMR Monthly Reports
Once the project begins, (identified by the pre-construction meeting) the Local Agency is required to submit a monthly report to the OSMR summarizing materials acceptance activities performed during that period. These reports are required regardless of whether any materials or source inspection related activities were performed by the SMR. If no activities were performed, a simple report will indicate that. Once SMR / Materials related activities are performed, the report will include all of the required information as listed in the SIQMP Outline Section 3.1 in Appendix 5.
Back to Table of Contents
16.
LOCAL AGENCIES AUDITS
The intent of the Independent Quality Assurance (IQA) audit is for METS to confirm that the Local Agency being audited is fulfilling commitments set forth in the approved SIQMP and contract documents. In general, the audit evaluates the Local Agency’s personnel, processes, and the overall effectiveness of their QA acceptance program for materials. The audit is not an inspection of a product or the acceptance of any material. As part of the cooperative agreement, Caltrans provides IQA to assure that materials acceptance work is performed by the Local Agency in compliance with the approved project plans, specifications, SIQMP and in accordance with Caltrans standards. To conduct this work, the OSMR is afforded access to all project work including source inspection activities and files. Although passing an audit does not guarantee that the Local Agency is in full compliance with its approved SIQMP, it documents that proper procedures are in place and there is a reasonable expectation that material quality adheres to the requirements of the contract documents.
16.1 Frequency
Audits typically occur once per quarter, however can increase or decrease in frequency should the OSMR deem necessary.
Factors to consider determining the frequency of the audits include:
-
SIQMP implementation
-
Local Agency’s past performance
-
Complexity and pace of the source inspection work
-
Review of Monthly Summary Reports
-
Findings from a previous audit
-
Overall level of cooperation and proactive stewardship
16.2 Documentation Auditing Activities
The audit will consist of an introductory meeting, review of QA verification procedures, interview of Local Agency’s project staff and a de-briefing meeting.
The review of the QA verification procedures includes:
- Nonconformance reports
- Inspection reports
- Material test reports
- Buy America verification
- Submittal review process
- Contractor submitted Quality Control Plans
Key project staff includes:
- Structural Material Representatives
- Inspection and testing staff
- Resident Engineer
- Structures Representative
16.3 Field Audits
The SMR should maintain close communication with the OSMR about scheduling for major fabrication items. METS will occasionally perform random audits at the facilities to verify that the Local Agency’s personnel are appropriately identified in the SIQMP, certified, qualified, and knowledgeable to perform the inspection.
16.4 Audit Report & Communication
The OSMR will compile the final notes and prepare a report with findings and a list of any concerns. The report will number each finding such that the resolutions of these findings are easily tracked throughout the project. The Local Agency is expected to respond to the IQA audit report within ten working days.
Sample IQA Audit Cover Letter can be found in Appendix 13.
Sample IQA Audit Report can be found in Appendix 14.
16.5 Closeout
As part of the closeout review, the OSMR will check the Monthly Summary Reports as well as any unresolved audit findings. If there are any outstanding audit findings, the Local Agency will work to resolve these findings before submitting a final acceptance letter. The Local Agency Resident Engineer is required, by the Section 3.2, “Final Acceptance Letter” of the SIQMP Outline in Appendix 5, to provide a stamped letter for the final materials acceptance and certification stating that the approved SIQMP procedures were followed during the life of the project. The OSMR will verify that this letter is on file.
If during the closeout review, the project was found to be in substantial compliance with the approved SIQMP and the project has no outstanding issues related to source inspection, then a “Closeout Action Letter” stating that the project is in compliance will be issued.
Unresolved findings that remain or are found during the time of the closeout review may result in the need for a letter to be issued. When it cannot be confirmed that work was performed in accordance with the approved SIQMP or there are outstanding issues on the project, the Closeout Action Letter will not be issued. Depending on the findings, appropriate stakeholders will be notified.
Back to Table of Contents
17.
LIST OF APPENDICES
1. Title 23 Code of Federal Regulations (CFR) Section 637.205
2. METS/GS Directive-03
3. Construction Procedure Directive 08-5 (CPD 08-5)
4. Deputy Directive 90 (DD-90)
5. The SIQMP Outline
6. Sample SIQMP
7. Risk Assessment Form deviating from high risk item
8. OSM Forms
9. Material List Requiring Source Inspection
10. Sample Identification Card
11. Material List Applicable Standards
12. SIQMP Approval Letter
13. IQA Audit Cover Letter
14. IQA Audit Report
15. NDT Requirement Reference
Back to Table of Contents
Appendix 1.
TITLE 23 CODE OF FEDERAL REGULATIONS (CFR) SECTION 367
Back to Table of Contents
Appendix 2.
METS-GS DIRECTIVE - 03
Back to Table of Contents
Appendix 3.
CONSTRUCTION PROCEDURE DIRECTIVE 08-5 (CPD 08-5)
Back to Table of Contents
Appendix 4.
DEPUTY DIRECTIVE 90 (DD-90)
Back to Table of Contents
Appendix 5.
THE SIQMP OUTLINE
Materials Engineering and Testing Services
Source Inspection Quality Management Plan (SIQMP)
Outline
For Use by Implementing Agencies on the State Highway System
IMAGE
Division of Engineering Services
Revision Date
03/06/15
State of California
Department of Transportation
Introduction
Policy
Per Caltrans Construction Procedure Directive (CPD) 08-5, and Deputy Directives 23-R1 and 90, when an agency other than Caltrans advertises, awards, and administers a project that is within the Caltrans right-of-way, a Construction Quality Management Plan (QMP) must be submitted by the agency for approval by Caltrans prior to issuance of any encroachment permits. If the implementing agency is providing verification source inspection, CPD 08-5 requires the implementing agency to prepare a separate Source Inspection Quality Management Plan (SIQMP).
Quality is an important element of successful project delivery. Caltrans has developed policies, procedures, and guidelines5-10 to facilitate the mandatory compliance with the Federal Highway Administration (FHWA) Title 23 requirements. Within Title 23, the FHWA
describes Quality Assurance (QA) of materials for construction projects The State Materials Engineer must approve the Source Inspection Quality Management Plan (SIQMP) prior to issuance of the encroachment permit for construction. The State Materials Engineer has delegated this authority to the Office of Structural Materials (OSM).
Purpose
This document was created to assist the implementing agency in the development of their SIQMP, as it relates to all materials manufactured or fabricated away from the jobsite. The SIQMP outline provides a template that implementing agencies can use to describe their QA Acceptance Program. This includes verification source inspection and material acceptance activities. This document brings relevant information together from many Caltrans references for the convenience of the implementing agency. The implementing agency should provide a SIQMP approximately equivalent to that of Caltrans9. To eliminate any perceived conflict of interest the implementing agency must not delegate verification inspection, sampling and testing responsibilities to the Contractor.
SIQMP Implementation
The OSMR will review the implementing agency’s SIQMP. In order to expedite the review and approval of the SIQMP, OSM will require the most current Plans and Specifications for the project be submitted along with the cooperative agreement. Once approved in writing, the SIQMP will be the guiding document for management of materials that are fabricated or produced outside of the jobsite.
The Contractor must perform quality control as outlined in the project documents. The implementing agency’s QA Acceptance Program consists of acceptance activities, independent of the Contractor, which include:
Verification of Contractor’s QC process
Verification inspection
Verification sampling and testing
Caltrans OSM will perform independent quality assurance (IQA) through periodic audits to ensure that the approved acceptance activities outlined in the SIQMP are followed.
OSM will communicate the IQA audit findings through periodic status reports submitted to the Oversight Engineer. These reports are based on an evaluation of the implementing agency’s adherence to the SIQMP. They will describe and track any SIQMP deviations. Upon completion of the source inspection activities and resolution of all outstanding IQA findings, OSM will provide a written letter stating that the project is in compliance with the approved SIQMP.
SIQMP Outline
It is recommended that the SIQMP be divided into the following three sections:
1. Project General Description ..............................................................................................................................................................5
2. Materials Management......................................................................................................................................................................5
2.1. Roles and Responsibilities ..................................................................................................................................................6
2.2. Verification Source Inspection and Documentation..............................................................................................................8
2.3. Verification Lab Testing and Documentation .......................................................................................................................9
2.4. Contractor Quality Control Plans .........................................................................................................................................9
2.5. Issue Resolution.................................................................................................................................................................10
3. Reporting QA Verification Documentation to Caltrans IQA .............................................................................................................11
3.1. Monthly Summary Report ..................................................................................................................................................11
3.2. Final Acceptance Letter......................................................................................................................................................11
Appendices .........................................................................................................................................................................................12
1. Definitions .............................................................................................................................................................................12
2. Template for Materials Verification Testing List......................................................................................................................19
3. References ............................................................................................................................................................................20
Below is a recommended breakdown of each section with example sub-sections to help the implementing agency produce an effective SIQMP. OSM will review the SIQMP, which defines the implementing agency’s verification source inspection for compliance with general industry standards and practices.
1. Project General Description
The intent of this section is to provide the project’s basic information. This information will provide the foundation for efficient IQA by Caltrans.
1.1 Indicate the planned advertise, award, and completion dates
1.2 Indicate the Caltrans Standard Plans and Specifications editions to be used
1.3 Description of funding source(s) and applicability of Buy America provisions
1.4 Provide a copy of the Cooperative Agreement
1.5 Provide scope of work to include at a minimum the following:
- Number and type of structures
- Engineer’s estimate
- Project Limits
1.6 Describe the anticipated phasing, including the timeline for each phase, and main items of work to be completed in each phase of work.
2. Materials Management
The goal of this section is to provide the implementing agency the opportunity and flexibility to describe their materials management process. Some of the typical references are provided in Appendix 5, References, for the benefit of the implementing agency.
Source inspection is an integral part of an effective QA Acceptance Program. Verification source inspection helps to ensure that structural materials incorporated into the State Highway System comply with contract requirements with regard to raw materials, fabrication processes, personnel certifications, and in-process QC testing. The purpose of verification source inspection is to:
- Verify that adequate off-site QC is in place
- Perform verification sampling and testing of representative material
- Perform necessary in-process verification inspections
- Perform Non-Destructive Testing at appropriate times
- Mitigate issues before the material is shipped to the jobsite
- Decrease the potential for project delays that verification sampling at the jobsite may cause
A QA Acceptance Program includes an assessment of all materials based on importance. The appropriate level of source inspection is conducted based on this assessment. As an example, materials with a higher consequence of failure may require source inspection 100% of the time while materials with less risk require less frequent inspection. The goal of this section is for the implementing agency to describe their verification source inspection process.
2.1. Roles and Responsibilities
Provide an organizational chart of the key positions to be filled by the implementing agency and Contractor. An acceptable framework is shown on Figure 2. Provide supporting documents with the names, certifications, licenses, and responsibilities for each position. When applicable, the documentation should include:
i. Professional Engineer (PE) serving as Agency Resident Engineer or equivalent
ii. Agency Assistant Resident Engineers or equivalent
iii. PE serving as Agency Structure Representative or equivalent
iv. Agency Assistant Structure Representative or equivalent
v. PE serving as Agency Structural Materials Representative or equivalent
vi. Agency Source Inspectors for Precast Concrete (PE or PCI Level II)
vii. Agency Steel Inspectors (CWI)
viii. Agency Non-Destructive Steel Inspectors (ASNT TC1A Level II)
ix. Agency Coatings Inspectors (NACE certified)
Provide the following information, when available:
x. Contractor’s Quality Control Manager
xi. Contractor’s Quality Control Concrete Inspectors (PE or PCI Level II)
xii. Contractor’s Quality Control Source Steel Inspectors (CWI)
xiii. Contractor’s Non-Destructive Steel Inspectors (ASNT TC1A Level II)
xiv. Contractor’s Coatings Inspectors (NACE certified)
IMAGE
2.2. Verification Source Inspection and Documentation
The implementing agency should categorize materials based on the level of importance for their project and should determine the appropriate level of source inspection required.
2.2.1 Describe the system used to identify which products will be source inspected by the agency (for example, all structural items categorized as “catastrophic consequences of failure” or “significant safety concerns” should be source inspected by the agency, while less critical items may be source inspected only on a periodic basis or inspected on site).
2.2.2 Describe the process by which fabrication facilities or materials are evaluated or pre-qualified for the project. Note: The use of Caltrans approved programs is at the discretion of the implementing agency. The implementing agency assumes all responsibility for material coming from these facilities. Also note that for Caltrans implemented projects additional QA processes are employed at these facilities in order to accept source inspected materials.
2.2.3 Provide a complete list of materials in a table with estimated quantities that are used in Caltrans right of way (ROW). For each material indicate whether it is inspected/sampled at the source and/or in the field.
2.2.4 For materials inspected/sampled at the source, provide frequency of verification inspection/sampling at the source and general source inspection procedure.
2.2.5 Identify any specialty materials for this project (e.g. proprietary systems).
2.2.6 Describe any items that are outside of the Caltrans ROW that will meet different criteria than this SIQMP outline and how items in Caltrans ROW will be distinguished and separated.
2.2.7 Describe the process by which the Contractor notifies the agency of suppliers/fabricators for each material item that requires source inspection.
2.2.8 Documentation: Every inspection must be documented and a report produced. Systematic documentation is a key component of the QA Acceptance Program. Documentation provides necessary information for IQA audits as well as any
future audits by FHWA, etc. In order to facilitate these audits, documentation needs to be organized and easily accessible.
2.2.8a Include the following sample forms:
i. Verification inspection forms including:
-
Source inspection/material verification
-
Verification sampling of material
-
Precast Reports
-
Welding Reports
-
Non-Destructive Testing Reports
-
Issues/Non-conformance Reports
-
Issue/Non-conformance Resolution Reports
-
Others as needed
ii. Verification compliance forms and/or material acceptance forms
2.2.8b Describe the procedures for review and distribution of inspection and material release forms
2.2.8c Describe how the implementing agency will perform final materials acceptance and certify that the approved SIQMP procedures were followed during the life of the project
2.2.8d Describe the materials filing system and the physical location it may be reviewed during audits
2.3. Verification Lab Testing and Documentation
A verification sampling and testing program must be established by the implementing agency. In order to avoid an appearance of a conflict of interest, any qualified private laboratory shall perform only one of the following types of testing on the same project: Verification testing, QC testing, or dispute resolution testing.
2.3.1 Describe verification lab qualifications for the applicable materials on this project (e.g. ISO 17025 for steel, and AASHTO Accreditation Program (AAP) for concrete).
2.3.2 Provide a list of verification tests to be performed by the implementing agency along with the frequency and applicable industry standards to be used/specified (ASTM, CTM, etc.). A template for the list is provided in Appendix 4.
2.3.3 Describe the verification materials testing filing system and the physical location it may be reviewed during audits.
2.3.4 Provide example forms that will be used for sampling material and reporting test results.
2.3.5 Provide a statement that there are no conflicts of interest regarding the verification lab and any other acceptance activities for the project.
2.4. Contractor Quality Control Plans
Part of an effective QA Acceptance Program is to assure that an effective Contractor QC Program is in place. QC Plans are an important part of a QC Program as they help to ensure the Contractor is following project requirements with regard to material, fabrication, testing, and inspection practices.
2.4.1. Generate a detailed procedure for implementing agency’s review of QC plans including:
i. Indicate the individual responsible for performing each review
ii. Documentation of the reviews and addendums (e.g. example forms)
iii. Filing of the reviews and addendums
2.4.2. For each activity/process listed below, a pre-operation meeting is typically specified in Caltrans specifications to verify the Contractor understands his role in the QC process, the flow of information is understood, and the schedule of activities is determined by:
- Welding and Non-Destructive Testing
- Precasting
- Painting
- Other special operations
For the meetings noted above, please provide the following details:
- Who is required to attend the pre-operation meetings
- Type of meeting (teleconference, in person, video conference, etc.)
- Goal of each type of meeting
- Method of filing the meeting minutes
2.5. Issue Resolution
A thorough QA Acceptance Program includes guidelines for issue resolution. The implementing agency should provide a description of their issue resolution process, how it is concluded, and how it is documented.
2.5.1 Describe the process for issues resolution (such as requests for information (RFIs), nonconformance reports (NCRs), or deviations to the contract related to source inspection) including:
Procedures for notification to the source, owner’s and contractor’s inspection staff
Procedures for documenting decisions
2.5.2 Describe when the unit responsible for verification activities is required to write non-conformance reports (NCRs) to document issues related to:
Product
QC Processes
2.5.3 Describe the policy and/or procedures for handling a disagreement between owner’s and contractor’s inspection staff.
3. Reporting QA Verification Documentation to Caltrans IQA
3.1. Monthly Summary Report
On the 1st of each month the implementing agency must produce a SIQMP Monthly Summary Report that describes the materials acceptance activities performed for that period. The report should be sent to the Oversight Structural Materials Representative (OSMR) for the project. The following link contains the latest OSM contact information.
The report will include at a minimum the following:
i. A statement verifying continued compliance with the SIQMP signed by the implementing agency
ii. Response to Caltrans IQA audit findings
iii. Summary of verification source inspection work completed over the reporting period and summary of work anticipated in the next period
iv. Summary of NCRs issued and status of those outstanding
v. Summary of any changes to the plans or specifications
During an audit the supporting documentation is to be provided within 10 working days. Examples of supporting documentation include:
Verification NCRs
Verification inspection reports
Material Test Reports (MTRs) by the Contractor
Certificates of Compliance (COCs) by the Contractor
Implementing agency submittal review comments for:
3.2. Final Acceptance Letter
The implementing agency Resident Engineer shall provide a stamped letter for the final materials acceptance and certification stating that the approved SIQMP procedures were followed during the life of the project.
SUMMARY
It is the intent of OSM to assist the implementing agency in adopting a meaningful materials management system that includes inspection, sampling, and testing both by the Contractor through QC and by the implementing agency through verification activities. Cooperation between the implementing agency and Caltrans helps insure materials quality resulting in on time and within budget project delivery. The SIQMP provides a platform for the implementing agency to incorporate effective material management strategies and communicate them to Caltrans
Appendices
Appendix 1: Definitions
Appendix 2: Template for Materials Verification Testing List
Appendix 3: References
1. Definitions
Contractor - The Prime Contractor, responsible for the construction of the project.
Cooperative Agreement (Co-op) - A formal, legally binding contract between Caltrans and the Implementing Agency. Cooperative agreements outline responsibilities and respective obligations, including cost sharing, of the participants and may address more than just the project construction. Cooperative agreements and maintenance or ownership obligations are required when exchanges of funds or commitments of resources occur. Once signed by an authorized representative of the other party and an attorney representing Caltrans, the agreement becomes legally binding and becomes the highest authority in the hierarchy of contract documents.
CPD 08-5 - Construction Procedure Directive regarding Quality Management Work on State Highway Systems.
Design-Bid-Build - Refers to the standard Caltrans project whereby Caltrans does the design of the project, and the project is awarded to a bidding contractor who will then construct the project.
Design-Build - Refers to a project where the Contractor is responsible for both the design and construction of the project.
Encroachment Permit - A permit issued by Caltrans granting permissive authority to enter the state right-of-way and construct approved facilities. An encroachment permit is an enforceable contract when accepted by the permittee. Acceptance of all terms of the encroachment permit is acknowledged when any act or work specified under the permit is performed. An encroachment permit does not convey a real property right. It authorizes only the permittee or permittee’s agent to perform work within the state right-of-way. The permittee may not transfer or assign an encroachment permit to another party. The Implementing Agency and the contractor performing the work require dual permitting. The structure representative obtains copies of encroachment permits from the Implementing Agency project manager or the resident engineer. As part of a cooperative agreement, encroachment permits are typically required as a means to perform construction activities in Caltrans right of way.
Federal-aid Project - Any project that has received any funding from the Federal Highway Administration (FHWA).
Final Acceptance Report – A report produced by the Oversight Resident Engineer for the implementing agency stating acceptable completion of the project. This final acceptance report is based on OSM’s final report recommending acceptance of the project for Structural Material related work.
Highway improvement agreement – Essentially a highway improvement agreement is a cooperative agreement with a private entity. Highway improvement agreements are not covered in this outline.
Implementing agency - The entity charged with the successful completion of each project component, as defined in Government Code Section 14529(b):
Project initiation document.
Completion of all permits and environmental studies.
Preparation of plans, specifications, and estimates.
The acquisition of right-of-ways, including, but not limited to, support activities.
Construction, construction management, and engineering including surveys and inspection.
There could be a different implementing agency for each component of a project. To ensure clear lines of responsibility, only one agency can be the implementing agency for a single component.
Independent Assurance (IA) - Management tool that requires a third party, not directly responsible for process control or acceptance, to provide an independent assessment of the product and/or the reliability of test results obtained from the process control and acceptance testing. (The results of IA tests are not to be used as the basis of product acceptance.) This definition differs from that of 23 CFR 637, which defines IA programs as “activities that are an unbiased and independent evaluation of all sampling and testing procedures used in the acceptance program.”
Independent Quality Assurance (IQA) - Activities performed by Caltrans at a project level to ensure that the implementing agency’s quality-assurance activities result in projects being developed in accordance with Caltrans standards, policies, and practices and in accordance with the QMP provided by the implementing agency.
Local Agency - Any public entity such as a federal, state, or regional transportation planning agency, county, city, or other local government unit that sponsors or administers a construction contract on the state highway system. In addition, a private entity that sponsors or administers construction contracts on behalf of an agency on the state highway system, unless otherwise noted, is considered a part of the local agency for the purpose of this guideline.
METS - Caltrans Materials Engineering and Testing Services.
Office of Structural Materials (OSM) – An office within Materials Engineering and Testing Services (METS). The primary objective of OSM is to provide uniform objective quality assurance evaluations of a large number of structural materials and other products that are a vital part of highways and bridges.
OSM Oversight Activity Report - An intermittent report that communicates OSM’s IQA activities, findings, and the status of all issues.
Oversight Engineer (OSE) - A Caltrans employee who performs independent quality assurance of the activities being performed by the resident engineer, the local agency structure representative, and others assigned to a construction project. The Oversight Engineer is the local agency’s primary Caltrans contact. The Oversight Engineer assures compliance with applicable state and federal regulations, contract requirements, Caltrans standards and practices, encroachment permit, and cooperative-agreement requirements. For federal-aid projects, the Oversight Engineer performs independent quality assurance of the quality assurance work performed by the local agency for the entire project. For non-federal-aid projects, the Oversight Engineer performs independent quality assurance on only the portion of the project within the existing or future state right-of-way. The Oversight Resident Engineer and Oversight Structure Representative are examples of Oversight Engineers.
Oversight Non-Conformance Report - A report issued by the Oversight RE to the implementing agency that reports deviations from the QMP. A resolution is required to close out the issue.
Oversight Project - Any project with a construction cost within the existing or future state highway right-of-way of $300,000 or greater where the local agency administers the construction contract. Oversight projects are financed in whole or in part by a local agency. Oversight projects with an estimated construction cost of $1 million or more are constructed under the terms of a cooperative agreement and encroachment permit. Most oversight projects with an estimated construction cost of less than $1 million are constructed under the terms of an encroachment permit only. Certain projects such as those involving signal construction, landscaping, or sound walls, may require an agreement.
Oversight Structural Materials Representative (OSMR) - A Caltrans Office of Structural Materials employee who is assigned to assist the OSE with IQA activities.
Oversight Structure Representative - An employee of Caltrans Office of Structures Construction who assists the Oversight Engineer in performing oversight over the implementing agency structure representative’s activities relative to structure portions of a project.
Quality Assurance (QA) - Table 1 shows a variety of definitions used for QA. For the purpose of this document the definition provided by the Code of Federal Regulations (23 CFR 637B) is used.
Table 1 — Various Definitions for Quality Assurance and Quality Control
Term |
23CFR637B |
Construction Manual Supplement for Local Agency's Resident Engineers (LARE) |
ACI (ACI Concrete Terminology, August 2010) |
Quality Assurance |
All those planned and systematic actions necessary to provide confidence that a product or service will satisfy given requirements for quality. |
Activities performed within the implementing agency during the project-delivery process that provides the confidence that the project team is fulfilling established project requirements and expectations. |
Actions taken by an organization to provide and document assurance that what is being provided are in accordance with the contract documents and standards of good practice for the work. |
Quality Control |
All contractor/vendor operational techniques and activities that are performed or conducted to fulfill the contract requirements. |
Operational processes, practices, and activities performed at the project team level during the project delivery process to ensure that the product meets the project's purpose and need and fulfills established quality requirements. |
Actions taken by an organization to provide control and documentation over what is being provided so that the applicable standard of good practice and the contract documents for the work are followed. |
Quality Assurance Acceptance Program – All factors that comprise the implementing agency’s determination of the quality of the product as specified in the contract requirements. These factors include verification sampling, testing, and inspection and may include results of quality control sampling and testing.
Quality Control (QC) - Table 1 shows a variety of definitions used for QC. For the purpose of this document the definition provided by the Code of Federal Regulations (23 CFR 637B) is used.
Quality Management Plan (QMP) - Per CPD 08-5, when an agency other than Caltrans advertises, awards, and administers a project that is within the Caltrans right-of-way, a Quality Management Plan (QMP) must be submitted by the agency for approval by Caltrans prior to issuance of the encroachment permit. If the implementing agency is providing its own source inspection, CPD 08-5 requires the implementing agency to prepare a separate Source Inspection Quality Management Plan (SIQMP). The State Materials Engineer, or authorized delegate (Quality Assurance and Source Inspection Senior), must approve the SIQMP prior to issuance of the encroachment permit for construction.
Resident Engineer - Use in the same context as described within the Construction Manual, except, the resident engineer works for the implementing agency, not Caltrans. Resident engineer performs jobsite verification sampling, testing and inspection of the contractor’s QC operations.
Source Inspection Quality Management Plan (SIQMP) – A Quality Management Plan specific to Quality Assurance Source Inspection that is developed by the implementing agency. As stated in Construction Procedure Directive (CPD) 08-5, this document must be approved by the State Materials Engineer before an encroachment permit can be granted.
Verification – Sampling, testing, and inspection performed to validate the quality of the product.
2. Template for Materials Verification Testing List
Material |
Amount of Material to be Tested |
Samples Taken |
Tests Performed |
1. Prestressing Steel Strand |
2 Strand Packs |
1 |
ASTM A370
ASTM E8
|
2. High Strength Fasteners |
Lot size: 281-500 assemblies |
5 |
ANSI/ASME B1.2
ASTM A 370
ASTM B 499
ASTM E 8
ASTM E 10
ASTM E 18
ASTM F 606
|
3. Mechanical Couplers |
Lot size: 150 |
4 |
ASTM A 370
ASTM E 8
CT 670
|
4. |
|
|
|
5. |
|
|
|
6. |
|
|
|
7. |
|
|
|
3. References
1. CFR Title 23
2. Construction Procedure Directive (CPD) 8-5: Quality Management Work on the State Highway System
3. Deputy Directive DD-23-R1, Roles and Responsibilities for Development of Projects on the State Highway System
4. Deputy Directive DD-90, Funding of Quality Management Work on State Highway Projects
5. Construction Policy Bulletin (CPB) 9-6: Oversight Project Completion Checklist
a. CEM-6302 Final Materials Certification
b. CEM-6303 Final Acceptance Checklist for Federal-Aid High Profile Projects
6. Construction Manual Supplement for Local Agency Resident Engineers (LARE)
7. Local Assistance Procedures Manual (LAPM)
8. Local Agency Structure Representative Guidelines (LASR)
9. Office of Structural Materials Practices and Procedures (OSMPP)
10. Oversight Field Engineers Guidelines
Some of these documents discuss the option for Caltrans to perform verification source inspection for an outside implementing agency. However, this happens very infrequently and must be established with the Chief of Office of Structural Materials prior to issuing the cooperative agreement.
Below is a summary of the documents and information on how to access them.
1. CFR Title 23:
From Title 23 FHWA Subchapter A – General Management and Administration:
“The purpose of the regulations in this part is to implement and carry out the provisions of Federal law relating to the administration of Federal aid for highways.”
This regulation outlines the State Transportation Department’s requirement to develop a QA Acceptance Program which will assure that the materials and workmanship incorporated into each Federal-aid highway construction project on the National Highway System are in conformity with the requirements of the approved plans and specifications, including approved changes.
2. CPD 8-5: Quality Management Work on the State Highway System
On August 20, 2008, the Construction Procedure Directive (CPD) 08-5 was signed in order to provide guidance for Quality Management Work on the State Highway System.
This CPD states that when a government agency or private entity is the implementing agency (i.e. the entity that advertises, awards, and administers the construction contract), Caltrans performs Independent Quality Assurance (IQA) services to ensure that quality management work is performed by the implementing agency as mandated by FHWA.
The CPD states the implementing agency should prepare and submit a separate source inspection Quality Management Plan. The State Materials Engineer must approve each source inspection quality management plan prior to issuance of the encroachment permit for construction. The State Materials Engineer will ensure that the implementing agency has prepared a quality management plan conforming to Caltrans standards.
3. Deputy Directive 23-R1: Roles and Responsibilities for Development of Projects on the State Highway System
4. Deputy Directive 90: Funding of Quality Management Work on State Highway Projects
5. CPB 9-6: Oversight Project Completion Checklist
Per CPB 9-6:
“Caltrans, the local agency, and the contractor review a locally administered state highway construction project before contract acceptance. This review identifies and then allows the contractor to address discrepancies before demobilizing and allows the local agency to avoid remobilization costs.”
Link to referenced forms:
6. Construction Manual Supplement for Local Agency Resident Engineers (LARE)
Per LARE:
“The Construction Manual establishes policies and procedures for personnel engaged in contract administration. However, not all policies and procedures in the Construction Manual are applicable to local agencies or private entities when advertising, awarding, and administering projects. This supplement establishes which sections of the Construction Manual are applicable to local agency and private entity projects.”
7. Local Assistance Procedures Manual (LAPM)
Per LAPM:
“The Local Assistance Procedures Manual (LAPM) has been prepared to aid California local agencies scope, organize, design, construct and maintain their public transportation facilities when they seek Federal Highway Administration (FHWA) funded federal-aid or state funding. This manual describes the processes, procedures, documents, authorizations, approvals and certifications, which are required in order to receive federal-aid and/or state funds for many types of local transportation projects.”
8. Local Agency Structure Representatives Guidelines (LASR)
Per LASR:
“The purpose of this guide is to provide structure representatives with an efficient resource to help them determine their roles and responsibilities in administering structure portions of local agency construction contracts built on state right-of-way.”
9. Office of Structural Materials – Quality Assurance and Source Inspection Branch (QASI) Manual
The OSM - QASI Manual is a manual that details the practices and procedures of the Office of Structural Materials – QASI Branch.
10. Oversight Field Engineer Guidelines (OFEG)
These guidelines provide a convenient source of information on policy and procedure, and should be used as a resource for Caltrans employees who provide IQA on projects administered by others on the existing or future state highway system.
Back to Table of Contents
Appendix 6.
SAMPLE SIQMP
Source Inspection Quality Management Plan
Sample City Main Street Bridge Replacement
Project No.: 123456
Caltrans EA: 07-XXXXX4
DRAFT FINAL
Prepared for:
Caltrans Materials Engineering and Testing Services (METS)
Attention: Caltrans Oversight Structural Materials Representative
October 18, 2012
Revision 0
Prepared by:
Sample City Materials and Testing Division (SC-MTD)
Table of Contents
Overview ...................................................................................................................................................................................4
1 Project General Description....................................................................................................................................................5
1.1 Project Planned Dates.....................................................................................................................................5
1.2 Project Specifications Edition ..........................................................................................................................5
1.3 Federal Funding Status ..................................................................................................................................5
1.4 Project Documents...........................................................................................................................................5
1.5 Scope of Work.................................................................................................................................................5
1.5.1 Description of Bridge Work ..........................................................................................................................6
1.6 Project Phasing................................................................................................................................................6
1.7 Additional Project Information...........................................................................................................................6
2 Material Management..............................................................................................................................................................7
2.1.1 Agency Roles and Responsibilities...............................................................................................................7
2.1.2 Contractor Information..................................................................................................................................9
2.2 Verification Source Inspection and Documentation....................................................................................................9
2.2.1 Procedure to Identify Materials for Source Inspection...................................................................................9
2.2.2 Authorized Materials and Audited Facilities List..........................................................................................10
2.2.3 List of Materials in the State Highway System Right-Of-Way (ROW) ..........................................................10
2.2.4 Table of Items to be Source Inspected........................................................................................................10
2.2.5 Special Materials – Proprietary Systems ....................................................................................................16
2.2.6 Project Materials Distinction........................................................................................................................17
2.2.7 Project Materials Management....................................................................................................................18
2.2.8 Documentation ...........................................................................................................................................18
2.3 Verification Lab Testing and Documentation ...........................................................................................................21
2.3.1 Qualification of the Verification Testing Laboratory......................................................................................21
2.3.2 List of Verification Tests and Frequencies...................................................................................................21
2.3.3 Verification Material Filing System...............................................................................................................25
2.3.4 Example Forms for Sampling and Testing...................................................................................................25
2.3.5 Verification/QC Testing Laboratory Conflict of Interests..............................................................................25
2.4 Contractor Quality Control Plans ............................................................................................................................25
2.4.1 Review of QC Plans ...................................................................................................................................25
2.4.2 Pre-Operation Meetings..............................................................................................................................26
2.5 Issue Resolution.......................................................................................................................................................27
2.5.1 CCOs, RFIs, and NCRs...............................................................................................................................27
2.5.2 Instances Requiring NCRs Materials: .........................................................................................................27
2.5.3 Procedures for Handling Disagreements ....................................................................................................29
3 Reporting Verification Inspection Status to Implementing Agency, Sample City.....................................................................29
3.1 Monthly Summary Report.........................................................................................................................................29
3.2 Final Acceptance Letter...........................................................................................................................................30
Appendices .................................................................................................................................................................................
Note: This Sample SIQMP contains no appendices. An actual SIQMP will contain appendices that have important required items such as sample forms, certifications for personnel and laboratories, or will contain added commentary on source inspection practices by the implementing agency.
This SIQMP is one example of source inspection practices and is not intended to direct local agencies with regard to how they approach source inspection.
Overview
This document is a sample Source Inspection Quality Management Plan (SIQMP) that was created to assist local implementing agencies with the development of a project specific SIQMP. Source Inspection relates to all materials manufactured or fabricated away from the jobsite that will be incorporated into the final work. The SIQMP outline found on the Agency Resources page of the Caltrans Materials Engineering and Testing Services website (http://www.dot.ca.gov/hq/esc/Translab/OSM/agencyresources.htm) provides an outline that implementing agencies can use to describe their QA source inspection and material acceptance activities. This Sample City SIQMP brings relevant information together from many Caltrans references for the convenience of the implementing agency and follows the SIQMP outline.
Where reference throughout this document is made to appendices, those are placeholders only as no sample appendices are included, e.g., no example personnel certifications or cooperative agreements. A final SIQMP for use on a project will be required to have the necessary supporting documents and/or appendices.
1 Project General Description
Table 1 presents the project general description.
Table 1: Project General Description.
Project Description |
Route 1 Main Street Bridge Replacement |
Implementing Agency Name |
City of Sample |
Implementing Agency Project Manager (PM) |
John F Kennedy |
Implementing Agency Project Number |
123456 |
Caltrans Project Number |
X7-XXXXX4 |
Project Route |
Route 1 |
1.1 Project Planned Dates
Table 2 presents project planned dates.
Table 2: Project Planned Dates.
Project Award Date |
10/10/2011 |
Project Advertised Date |
5/10/2011 |
Project Notice to Proceed |
11/10/2011 |
Project Completion Date |
11/10/2013 |
1.2 Project Specifications Edition
Table 3 presents the edition of project Standard Specifications and Plans.
Table 3: Project Specifications Edition
Caltrans Standard Specifications |
May 2006 with Amendments Dated 08-05-11 |
Caltrans Standard Plans |
2006 and Revisions |
1.3 Federal Funding Status
Table 4 presents project federal funding status.
Table 4: Project Federal Funding Status.
Federal Funding (Buy America Requirements) |
Federally Aided Project - Buy America requirements will be enforced. |
1.4 Project Documents
Table 5 lists the project documents.
Table 5: List of Project Documents Provided
Copy of Cooperative Agreement |
See Appendix A |
Project Bid Items List |
See Appendix B |
1.5 Scope of Work
Table 6 presents project scope of work.
Table 6: Project Scope of Work.
Number and Type of Structures |
Bridge replacement of one bridge with precast concrete I-girders and founded on steel pipe piles (Class N) and concrete piles, and construct 2100 LF of Soundwall of varying height along the Southbound Route 1 freeway. |
Engineer's Estimate
|
$23,345,678.00 |
Project Limits |
From 3 miles north on Route 1 and Sample River Overcrossing to 3 miles south of Route 1 and Main Street Undercrossing in Example County within Sample City. |
1.5.1 Description of Bridge Work
The bridge work is on the Sample City Main Street Bridge (Bridge # 12-2456) and consists, in general, of:
1. Removing the existing Sample City Main Street Bridge. This includes removal of the cast in place bridge pier walls, retaining walls, curtain walls, type 2 barrier railing, miscellaneous metal cable restrainers, rock slope protection, bike path railing and bike path concrete.
2. Constructing a new Sample City Main Street Bridge. This work includes constructing abutments built on steel pipe piles as well as concrete piles, and building the bridge deck on precast prestressed concrete girders and PTFE Spherical Bearings. Bridge Construction also includes new concrete barrier rail, constructing diaphragm stiffeners, constructing masonry block soundwalls, constructing concrete barrier rail, and installing “Decorativelight” brand poles (Sole source for this project).
Description of Existing Structure: A three-span reinforced concrete box girder and cast-in-place prestressed concrete box girder bridge on 6 column reinforced concrete bents and open end seated abutments, all supported on driven reinforced concrete and precast prestressed concrete piles.
Description of the Soundwall Work: The Soundwall work consists, in general, of constructing CIDH piling and a reinforced concrete pile cap and wall to support masonry block Soundwall.
1.6 Project Phasing
It is anticipated that this project would be completed in 4 phases. The phases and estimated timelines are as follows:
1. A temporary traffic and pedestrian detour to guide traffic along frontage roads to the South Sample City River Crossing Bridge near Z Street (1 week).
2. Partial bridge removal including pier walls, retaining walls and curtain walls (5 weeks).
3. Constructing new abutments built on steel pipe piles, installing PTFE Spherical Bearings, and precast I-girders (8 months).
4. Constructing masonry block, soundwalls, concrete barrier rail, and light pole installation (5 months).
1.7 Additional Project Information
Table 7 presents additional project information.
Table 7: Additional Project Information.
Name and Address of Construction Management Firm |
SEPMIN and Associates, Inc.
123 East Main St., Sample City, CA 90000
|
Name and Address of Verification Firm for Construction |
Sample City / SEPMIN and Associates, Inc.
123 East Main St., Sample City, CA 90000
|
Name and Address of Verification Lab for QA Source Inspection |
Sampletest Lab Company
11112 Central Main St., Sample City, CA 90000
|
Name and Address of Verification Firm for Source Inspection |
Sample City Materials and Testing Division
12121 H Street, Sample City, CA 90000
|
Name and Address of Contractor |
John Schmidt Construction Inc.
1234 West Main St., Sample City, CA 90000
|
2 Material Management
In accordance with FHWA Title 23 requirements, the Prime Contractor will perform Quality Control (QC) as outlined in the project specifications and Sample City will implement a Quality Assurance (QA) acceptance program consisting of verification activities that are independent of the Prime Contractor. Sample City Materials and Testing Division (SC-MTD) has created a comprehensive material priority list that is based upon the consequence of failure of materials. This priority list helps project Structural Materials Representatives (SMRs) to determine the level of source inspection required. The priority list is described under section 2.2.1 of this document.
2.1 Roles and Responsibilities
A project organizational chart specific to the construction phase quality management responsibilities for Source Inspection is provided in Figure 1.
2.1.1 Agency Roles and Responsibilities
To supplement Figure 1, Table 8 below presents a List of Sample City Project Personnel and Qualifications.
Table 8: List of Project Personnel and Qualifications
Title |
Name |
Qualification |
Company |
Phone |
Email |
Resident Engineer (RE) |
Grover Cleveland |
Professional Engineer (PE) Civil California |
Sample City / SEPMIN and Associates, Inc. |
(123) 456-7890 |
G.Cleveland@mail.com |
Structure Representative (SR) |
George Washington |
PE Civil CA |
Sample City |
(111) 222-3333 |
G.washington@mail.com |
Structural Materials Representative (SMR) |
Abraham Lincoln |
PE Civil CA |
Sample City |
(333) 111-2222 |
A.lincoln@mail.com |
Concrete QA Inspector |
John Adams |
PCI Level II |
Sample City |
(111) 222-4444 |
J.adams@mail.com |
Steel QC Inspector |
Tom Jefferson |
CWI |
Sample City |
(222) 444-5555 |
T.jefferson@mail.com |
NDT QC Inspectors |
James Polk |
ASNT NDT Level II UT |
Sample City |
(444) 555-8888 |
J.polk@mail.com |
Coating Inspector |
James Madison |
NACE Level II |
Sample City |
(777) 444-2233 |
J.madison@mail.com |
IMAGE
Figure 1: Construction Phase Quality Management Responsibilities for Source Inspection.
2.1.2 Contractor Information
Table 9 summarizes minimum Quality Control qualifications for Contractor personnel as required by the project Special Provisions:
Table 9: Minimum Qualification for Contractor’s QC Personnel
Quality Control Manager (QCM) - Precast |
Experienced in Quality Control and Concrete |
Quality Control Manager (QCM) - Steel |
AWS CWI or PE Civil CA |
Concrete QC Inspector |
PCI Level II or PE Civil CA |
Steel QC Inspector |
AWS CWI |
NDT QC Inspectors |
ASNT TC-1A Level II |
Coating QC Inspectors |
NACE Level II |
2.2 Verification Source Inspection and Documentation
2.2.1 Procedure to Identify Materials for Source Inspection
Sample City will follow a similar system to the Caltrans procedure for identifying items that will require Source Inspection. Sample City has generated a “Materials Priority list” as described previously in Section 2. Each material bid item has been categorized in table 10 and is supplemented by section 2.2.4.1 which details the frequency of verification inspection for source inspected items.
-
“Priority 1” materials are items with significant safety concern or high maintenance cost associated with a failure; these items normally have a QA inspector at the facility throughout the fabrication time period and a “tag” issued at completion along with a final inspection report. When multi-shift operations occur, either a single inspector will cover both shifts by splitting the shift, or multiple inspectors are assigned to ensure adequate quality assurance checks. Such inspection is considered “extensive” but inspectors are performing quality assurance checks only and are not required to be at the shop continuously. Priority 1 items are broken into Priority 1a, 1b, and 1c in section 2.2.4.1 where the source inspection process is more fully described.
-
“Priority 2” materials are items with moderate safety concern or moderate maintenance cost. Normally part time QA inspection (Spot checks of in-process work at a single or multiple times during the fabrication time period) is conducted. A tag is normally issued at completion of work along with a final inspection report.
-
“Priority 3” materials are items with low safety concern or low maintenance cost and normally require only field inspection and a Certificate of Compliance. Periodic spot checks may be made at the discretion of the SMR.
In addition to the material priority list, the following additional criteria is used to determine the frequency and extent of Source Inspection by the SMR:
-
Past performance of the fabricator (confidence in the QC process).
-
Special circumstances, e.g., (emergency or change order work) may require additional tracking/inspection.
-
Past issues with the product performance.
-
Unique or unusual characteristics or expectations.
-
Warranties: Items with a warranty will normally not require source inspection.
2.2.2 Authorized Materials and Audited Facilities List
For some materials, the project Special Provisions will require that the Contractor use Authorized Materials that are prequalified by Caltrans. The Sample City SMR may randomly sample materials that are provided on the project, including materials that are from Authorized Suppliers. In such cases, samples will be tested at the Sample City (or consultant lab hired by Sample City) accredited lab. Sample City is aware that the list of prequalified materials is accessible at the following link:
Where the Special Provisions require Caltrans audited facilities to be used, Sample City will require the Contractor to use such facilities for any materials provided on the project. In addition to the use of Caltrans audited facilities when required, Sample City has implemented a special procedure for any facilities that will be producing Priority 1 items. Once identified on a SC-3101 as a fabricator, the Sample City SMR will make a prefabrication visit to Priority 1 fabricators to conduct a pre-job audit. For Priority 2 items, the SMR may make a pre-fabrication visit. Sample City is aware that the list of audited facilities can be found at the following Caltrans link:
For proprietary lighting, see Section 2.2.5 of this document.
2.2.3 List of Materials in the State Highway System Right-Of-Way (ROW)
A complete list of materials that are within the Caltrans ROW along with the estimated quantities and location of inspection performed are provided in Table 10.
2.2.4 Table of Items to be Source Inspected
Frequency of source inspection is dependent upon the Priority of each item. Table 10 indicates the Priority of each item listed. Table 10 is supplemented by section 2.2.4.1 which further describes the frequency of inspection:
2.2.4.1 Frequency of Source Inspection
This section further defines the inspection frequency for priority 1, 2, and 3 items.
- Priority 1: “Priority 1” materials are items with significant safety concern or high maintenance cost associated with a failure. Sample City intends to send an audit team to conduct a facility assessment for each item identified as Priority 1 in Table 10 prior to the start of work. Some exceptions may be made to this if a facility is not performing a significant portion of the work. The primary purpose of this assessment is to discuss the source inspection process including the need for the fabricator to notify
Sample City in advance of the start of work, to discuss any required pre-meetings, to discuss the QC versus QA processes to be followed, and to identify any specific concerns of Sample City or the fabricator related to the product they will be supplying.
Priority 1a: Extensive QA Source Inspection
Priority 1a items on this project that have fabrication processes that are deemed as a high priority to see on an ongoing basis are the Class N Steel Pipe Piles, Truss Sign Structures and associated steel components, Precast/Prestressed Piles, and Precast/Prestressed Girders. For these items, a Sample City QA Inspector will be assigned to the fabrication facility on a full time basis to provide extensive QA coverage. While not required to be present during all shifts, in general where multi-shift operations occur, either a single inspector will cover both shifts by splitting the shift, or multiple inspectors are assigned to ensure adequate quality assurance checks. Such inspection is considered “extensive QA” but inspectors are performing quality assurance checks only and are not required to be at the shop continuously. In addition, Sample City considers field welding of the Class N piles and structural steel to require extensive inspection and are a specialty item. For this reason, Sample City’s Materials Department will perform field inspection on the Class N pile field welding operations.
Priority 1b: Priority 1 Items Requiring Source Inspection at Important Points Only
Priority 1b items that require inspection only during important points in the fabrication are: PTFE Spherical Bearings, Structural Steel Anchorages, and Light Poles. For PTFE Spherical Bearings, Sample City will send the SMR to select and witness the proof testing of the Bearings once complete. The SMR may choose to send an inspector during fabrication and/or painting of PTFE Bearings if not supplied by a company that is familiar with Caltrans Specifications or if other concerns arise. A final inspection and release of the product after all work and testing is complete will be performed at the source. For Structural Steel Anchorages, Sample City will select QA test samples for testing at the Sample City lab, return when such samples have passed, and “tag” the material to either the next process or jobsite. For Light Poles, Sample City will at a minimum send an inspector for QA final inspection of the product and review of QC records at the source with the exception of the Specialty Lighting identified in Table 10 and described in the footnotes of Table 10.
Priority 1c: Priority 1 Items that are Sampled at the Source
Priority 1c items on this project that require QA source sampling but not inspection on an extensive basis are High Strength fasteners and Couplers. Sample City will send a QA inspector to the facility to sample each lot of high strength fasteners in accordance with the following table:
Bolt Sampling Table.
Lot Size* |
Total Sample Size per Lot |
Source From:
a) New Foreign and Domestic manufacturers, and
b) Established foreign and domestic manufacturers with previous rejections.
|
Source From:
Established foreign and domestic manufacturers with past satisfactory quality.
|
No. of Samples Required per Lot |
No. of Samples Required per Lot |
2 to 15 |
3 |
1 |
16 to 25 |
4 |
1 |
16 to 50 |
5 |
1 |
51 to 90 |
7 |
3 |
91 to 150 |
8 |
3 |
151 to 280 |
9 |
3 |
280 to 3,200 |
12 |
5 |
3,201 to 10,000 |
12 |
7 |
10,001 to 35,000 |
16 |
7 |
35,001 to 150,000 |
16 |
8 |
150,001 to 500,000 |
16 |
10 |
500,001 + |
20 |
12 |
- Lot size shall be defined as the total number of fasteners from one production or assembly lot or shipment which is available for sampling and inspection at a particular time.
- One sample is defined as one of each of the fastener components (i.e. bolt, nut, washer, DTI, cap screw, etc.) that make up fastener assembly
Couplers: For couplers that are assembled in a shop, the QA inspector will witness the coupling and verify that QA and QC samples are sent to the respective labs. For couplers assembled in the field, no source inspection will be required as the field inspection staff will be responsible for QA and QC sampling and testing.
Table 10: Items to be used in the Caltrans Right-Of-Way
Bid # |
Bid Item |
Quantity |
Material |
Inspection Location |
Priority |
52 |
Cap Inlet |
LS |
All Components |
Field/COC |
3 |
53 |
Irrigation System |
LS |
All Components |
Field/COC |
3 |
54 |
8" Welded Steel Pipe Conduit |
1,200 LF |
All Components |
Field/COC |
3 |
55 |
Aggregate Base* |
20,400 CY |
All Components |
Field/COC |
3 |
56 |
Class 3 Aggregate Base* |
16,400 CY |
All Components |
Field/COC |
3 |
57 |
Lean Concrete Base Rapid Setting |
1,260 CY |
All Components |
Field/COC |
3 |
58 |
Concrete Pavement (Rapid Strength Concrete) |
15,400 CY |
All Components |
Field/COC |
3 |
59 |
16" CIDH Piling (Concrete) |
7,725 LF |
Couplers |
Source/Field |
1c |
Other Components |
Field/COC |
3 |
60 |
PTFE Spherical Bearing |
24 EA |
PTFE Bearing Components |
Source |
1b |
Painting of Bearings |
Source |
1b |
61 |
Structural Concrete Bridge |
10,125 CY |
Concrete* |
Field/COC |
3* |
Steel reinforcement** |
Field** |
3** |
Couplers |
Source/Field |
1c |
Other Components |
Field/COC |
3 |
62 |
Structural Concrete, Soundwall |
2,780 CY |
Concrete |
Field/COC |
3 |
Steel reinforcement** |
Field** |
3** |
Couplers |
Source/Field |
1c |
Other Components |
Field/COC |
3 |
63 |
Structural Concrete, Approach Slab |
988 CY |
Epoxy Coated Reinforcement |
Source |
2 |
Concrete |
Field/COC |
3 |
Other Components |
Field/COC |
3 |
64 |
Minor Concrete (Minor Structures) |
190 CY |
All Components |
Field/COC |
3 |
65 |
Minor Concrete (Pipe Encasement) |
42 CY |
All Components |
Field/COC |
3 |
66 |
Precast I-Girders |
24 EA |
Concrete* |
Source/COC |
3* |
Steel Strand System |
Source |
2 |
Steel reinforcement** |
Field** |
3** |
67 |
Drill and Bond Dowel |
720 LF |
All Components |
Field/COC |
3 |
69 |
Soundwall (Masonry Block) |
26,400 SQFT |
Masonry Block - High Strength |
Source |
2 |
70 |
Joint Seal (MR 1") |
288 LF |
Sealant |
Source |
2 |
Other Components |
Field/COC |
3 |
71 |
Steel Pipe Piles - Class N |
1,120 LF |
All Components |
Source |
1a |
72 |
Bar Reinforcing Steel (Bridge) |
3,159,500 LB |
All Components** |
Field |
3** |
73 |
Bar Reinforcing Steel (Soundwall) |
316,970 LB |
All Components** |
Field |
3** |
74 |
Misc. Bridge Metal |
42,700 LB |
Brackets for monitoring system |
Field/COC |
3 |
Anchorage System (Source Fabricated Components) |
Source |
1c |
High Strength Fastener |
Source |
1c |
Other misc bridge metal Fabrication - Welding |
Source |
2 |
Other Fabrication - Painting |
Source |
2 |
Other Fabrication - Galvanizing |
Source |
2 |
75 |
Furnish Sign Structure (Truss) |
36,850 LB |
Truss Fabrication |
Source |
1a |
Anchorage System (Source Fabricated Components) |
Source |
1c |
High Strength Fasteners |
Source |
1c |
Galvanizing |
Source |
2 |
Field Splice/Bolts |
Field/COC |
3 |
Other Components |
Field/COC |
3 |
76 |
Furnish Formed Panel Sign (Overhead) |
350 SQFT |
Panel |
Source |
2 |
Other Components |
Field/COC |
3 |
77 |
Furnish Single Sheet Aluminum Sign (0.08" Unframed) |
370 SQFT |
All Components |
Field/COC |
3 |
78 |
Furnish Single Sheet Aluminum Sign (0.08" Framed) |
330 SQFT |
All Components |
Field/COC |
3 |
79 |
"Welcome to Sample City" Illuminated Sign |
1EA |
Sign |
Field/COC |
3 |
Lighting*** |
Field/COC |
3*** |
80 |
Precast Prestressed Concrete Piles |
6,812 LF |
All Components |
Source |
1a |
81 |
Precast Drainage Inlets |
4 EA |
All Components |
Field/COC |
3 |
82 |
18" Reinforced Concrete Pipe |
500 LF |
All Components |
Field/COC |
3 |
83 |
72" Reinforced Concrete Pipe |
372 LF |
All Components |
Source |
2 |
84 |
Miscellaneous Iron and Steel |
19,544 LB |
Source Fabrication |
Source |
2 |
Anchorage Assembly |
Source |
2 |
Other Components |
Field/COC |
3 |
85 |
Transistion Railing (Type WB) |
1 EA |
All Components |
Field/COC |
3 |
86 |
MBGR Connection to Bridge Railing |
4 EA |
All Components |
Field/COC |
3 |
87 |
Decorative Steel Fence |
110 LF |
All Components |
Field/COC |
3 |
88 |
Concrete Barrier (Type 60W) |
520 LF |
All Components |
Field/COC |
3 |
89 |
Concrete Barrier (Type 60R) |
2,930 LF |
All Components |
Field/COC |
3 |
90 |
Concrete Barrier (Type 736M) |
420 LF |
All Components |
Field/COC |
3 |
91 |
Concrete Barrier (Type 736V) |
380 LF |
All Components |
Field/COC |
3 |
92 |
4" Thermoplastic Traffic Stripe |
32,600 LF |
Paint |
CHEM/LAB |
3 |
Other Components |
Field/COC |
3 |
93 |
8" Thermoplastic Traffic Stripe |
3,780 LF |
Paint |
CHEM/LAB |
3 |
Other Components |
Field/COC |
3 |
94 |
Thermoplastic Pavement Marking |
6,510 SQFT |
Adhesive |
CHEM/LAB |
3 |
Other Components |
Field/COC |
3 |
95 |
4" Thermoplastic Traffic Stripe (Broken) |
25,600 LF |
Paint |
CHEM/LAB |
3 |
Other Components |
Field/COC |
3 |
96 |
Pavement Marker (Non-Reflective) |
6,090 EA |
Adhesive |
CHEM/LAB |
3 |
Other Components |
Field/COC |
3 |
97 |
Pavement Marker (Retro-Reflective) |
3,110 EA |
Adhesive |
CHEM/LAB |
3 |
Other Components |
Field/COC |
3 |
98 |
Maintaining Existting Traffic Management System |
LS |
Electrical Components*** |
Field/COC |
3*** |
Other Components |
Field/COC |
3 |
99 |
Lighting (Temporary) |
LS |
Electrical Components*** |
Field/COC |
3*** |
Other Components |
Field/COC |
3*** |
100 |
Modify Communication System |
LS |
Electrical Components*** |
Field/COC |
3*** |
Other Components |
Field/COC |
3*** |
101 |
Modify Lighting and Sign Illumination |
LS |
Electrical Components*** |
Field/COC |
3*** |
Poles |
Source |
1b |
Anchor Rods |
Source |
1b |
Field Connection/Bolts (HS) |
Source |
1c |
Other Components |
Field/COC |
3 |
102 |
Custom Decorative Lighting |
LS |
Electrical Components*** |
Field/COC |
3 |
Decorative Poles**** |
WARRANTY**** |
WARRANTY |
Other Components**** |
WARRANTY**** |
WARRANTY |
Table 10 Notes:
*For Priority 1 and Priority 2 precast bid items with concrete, supplementary cementitious material and aggregates will be sampled and tested by the Sample City Material Testing Division prior to the start of work by those facilities. Field concrete operations including any sampling will be handled in accordance with the field Quality Management Plan and are not covered by this SIQMP.
**Sample City will make one trip to the Steel reinforcement Supplier(s) to verify the QC process used. This single visit may serve as the QA check for all the steel reinforcement on the project from a given facility at the discretion of the SMR.
***All electrical components for this job are State Furnished. As such, Sample City will perform a final visual inspection when they arrive and file any associated paperwork/COC’s but will not source inspect electrical components. Should a special order item be needed, Sample City will consult the SIQMP outline addendum maintained by the Caltrans Electrical Department and source inspect/test the items as appropriate.
**** The Decorative Poles will be a sole source material to ensure that they match the other lighting within Downtown Sample City. These items are under warranty and will be maintained by Sample City as stipulated in the cooperative agreement. As a result, these light poles will not be fabricated at a Caltrans Audited Facility. In addition, due to the warranty, Sample City does not intend to perform any source inspection of these items. Section 2.2.5 contains additional information on this lighting system.
2.2.5 Special Materials – Proprietary Systems
Proprietary “Decorativelight” brand lighting has been sole sourced to match other Sample City lighting near the
project location. This lighting is allowed per Contract Special Provisions:
These lights will be maintained by Sample City as a condition of the Cooperative Agreement.
2.2.6 Project Materials Distinction
Table 11 shows Items that are partially out of Caltrans Right-of-Way.
For consistency, Sample City intends to apply the same Priority system and inspection process to all materials for
this project, whether in Caltrans ROW or not.
Table 11: Items that are partially out of Caltrans Right-of-Way
Bid # |
Bid Item |
Material |
53 |
Irrigation System |
All Components |
69 |
Soundwall (Masonry Block) |
Masonry Block - High Strength |
Other Components |
73 |
Bar Reinforcing Steel (Soundwall) |
All Components |
84 |
Miscellaneous Iron and Steel |
Source Fabrication |
Anchorage (Source) |
Other Components |
92 |
4" Thermoplastic Traffic Stripe |
Paint |
Other Components |
93 |
8" Thermoplastic Traffic Stripe |
Paint |
Other Components |
94 |
Thermoplastic Pavement Marking |
Adhesive |
Other Components |
95 |
4" Thermoplastic Traffic Stripe (Broken) |
Paint |
Other Components |
96 |
Pavement Marker (Non-Reflective) |
Adhesive |
Other Components |
97 |
Pavement Marker (Retro-Reflective) |
Adhesive |
Other Components |
101 |
Modify Lighting and Sign Illumination |
Electrical Components |
Poles |
Anchor Rods |
Field Connection/Bolts |
Other Components |
102 |
Decorative Light Poles* |
All Components* |
* These light poles are a specialized product with a warranty as indicated in section 2.2.5, and as such, they will be maintained by Sample City inside and outside of the Caltrans ROW and will not be subject to audit or source inspection.
2.2.7 Project Materials Management
Sample City will utilize the same nomenclature as Caltrans for material management with slight exception as noted here; The RE will ensure that the Contractor will submit the SC-3101,"Notice of Materials to be Used" form for all the materials to be incorporated in the project. This form lists vendors and fabricators providing materials for the project. Upon receipt of each SC-3101 form, the SMR will determine, based on Sample City’s Prioritization procedure described in Section 2.2.1 of this document, whether the material listed requires inspection at: 1) the source by Sample City’s Materials Division or 2) field by Construction.
1. Source Inspection: If material listed on the SC-3101 form requires Source Inspection, the SMR or responsible Sample City Material Division will send a Sample City Form-608 "Notice of Materials to be Furnished" to the vendor or fabricator, Prime Contractor and Resident Engineer. This document informs all parties that Sample City will perform inspection and release of material prior to being sent to the jobsite. A “Sample City Form-38”, Inspection Request Form, is included with the Sample City Form 608 sent to the vendor or fabricator. The vendor or fabricator then faxes the “Sample City Form-38” back to the Sample City Materials Division to request an inspection date.
When materials are issued a “Sample City Form-608”, the Sample City Materials Division will dispatch inspectors to carry out inspection activities as outlined in this SIQMP.
2. Field Inspection: If the material listed on the SC-3101 form does not require Source Inspection, (Priority 3) the inspection is assigned to the Resident Engineer at the job site through the use of Sample City Form- 28, "Notice of Materials to be inspected." The Prime Contractor and vendors are also sent a copy of the “Sample City Form-28” in order to inform them that Source Inspection is not required prior to shipment to the jobsite.
2.2.8 Documentation
Sample City Inspectors will document the daily QA Inspection activity for the project. Sample QA inspection forms are included in the Appendix E.
- Material Management
- Inspection Request
- Material Release
- Source Inspection Reports
- Non Conformance reports
- Review Forms
2.2.8.1 Included are the Following Sample Forms:
i. Note, the following forms required of the SIQMP are discussed above in 2.2.8, and are included in the appendix section. Several forms are repeated in more than one category below as they pertain to multiple functions. Forms required for inspections are:
- Source Inspection/Material Verification
- Sample City Form-29 Report of Inspection of Material (Sample City Orange Tag)
- Sample City Form-6011 Component Material Inspection Report (Sample City Green Tag)
- Sample City Form-6012 Stock Material Verification
- Sample City Form-6014 Report of Verification of Material (Sample City Blue Tag)
- Sample City Form-6034 Source Inspections Report
- Sample City Form-6042 Paint Inspection Report
- Sampling of Materials for Testing
-Sample City Form-0101 Sample Identification Card
- Sample City Form-6033 Precast Concrete Inspection Form
- Sample City Form - Review of Precast Concrete Quality Control Plan
- Sample City Form-23 Review of Contractor’s Welding Quality Control Plan
- Sample City Form-6031 Welding Inspection Reports
- Sample City Form-6032 Welding Witness Report
- Sample City Form-22 Review of Paint Quality Work Plan
- Sample City Form-6042 Paint Inspection Report
- Non-Destructive Testing Reports
- Sample City Form-6027 Ultrasonic Testing (NDT)
- Sample City Form-6028 Magnetic Particle Testing (NDT)
- Issue/Non-Conformance and Non-Conformance Resolution Reports
- Sample City Form-15 Non Conformance Report
- Sample City Form-16 Non Conformance Resolution
- SC-3101 Notice of Materials to be Used
- Sample City Form-28 Notice of Materials to be Inspected
- Sample City Form-608 Notice of Materials to be Furnished
- Sample City Form-38 Inspection Request Form
ii. Note: Compliance certification forms and/or material verification forms required of the SIQMP are included are included in the appendix.
- Sample City Form-29 Report of Inspection of Material (Sample City Orange Tag)
- Sample City Form-6011 Component Material Inspection Report (Sample City Green Tag)
- Sample City Form-6013 Material Suitability Report (Accompanies a Sample City Blue Tag and Sample City Form 6014)
- Sample City Form-6014 Report of Verification of Material (Sample City Blue Tag)
2.2.8.2 Review and Distribution of the QA Inspection Reports
Upon completion of each report, the inspector will send the inspection report(s) to a Reviewer. The Reviewer will transmit the reviewed inspection reports to the Sample City RE/SR. These reports will be filed and available to the Caltrans OSMR upon request or during an audit.
2.2.8.3 Material Acceptance
Materials Acceptance depends upon “materials releases” from the point of source inspection, obtaining proper certifications from the Contractor and performing a field inspection for items to be inspected in the field, and following this Source Inspection Quality Management Plan.
The following generally describes the material release process for items that are source inspected: If the material conforms to the Project Specifications and is intended to be shipped to the jobsite, the QA Inspector will release the material with a “Sample City Orange Tag” and will issue a “Sample City Form-29” Report of Inspection of Materials. If the material has been inspected at one fabricator and is intended to go to another fabricator for further fabrication, the QA Inspector will release the material with a “Sample City Green Tag” and will issue a Sample City Form-6011 Component Material Inspection Report Form. If the material complies with other documents such as an RFI, Sample City memorandum, or other forms of communications, and the Sample City SMR and Sample City RE agree that the material is fit for purpose, then the QA Inspector will release the material with a” Sample City Blue Tag” and will issue a Sample City Form-6014 “Report of Verification of Material Form”. See Section 2.5.2.4.1of this document for details about Sample City Blue Tag. Sample City will obtain concurrence from the Oversight RE for such changes as required per the responsibilities outlined in the cooperative agreement.
For items that are to be field inspected, the RE will obtain a Certificate of Compliance from the Contractor and have a field inspection conducted by a field Engineer or Inspector from Sample City.
At project closeout, Sample City’s Resident Engineer will be responsible for performing final materials acceptance and certify that the approved Quality Management Program (QMP) procedures were followed during the life of the project with a final acceptance letter provided to Sample City.
2.2.8.4 Inspection Report Filing
All Sample City Materials Division Inspection Report Forms and documents will be distributed to the Sample City RE/SR. The reports will be available to the OSMR at any time. Storage of these hard copy reports will be kept at the Sample City Material Division at the following address:
Sample City Materials Division
1 Main Street,
Sample City, CA 90000
Phone: (111) 111-1111
FAX (222) 222-2222
2.3 Verification Lab Testing and Documentation
2.3.1 Qualification of the Verification Testing Laboratory
Steel Testing will be performed by Sampletest, Inc. This laboratory is accredited by the American Association for Laboratory Accreditation (A2LA) for rubber products testing, steel/iron testing, fastener testing, prestressing steel strand, hardness, spliced reinforcing steel, epoxy coating, wire mesh, metallography, carbon steel chain, wire rope, and dimensional testing.
Additional tests that are required by the project specifications, such as concrete material testing will be performed by one of the three AASHTO Accreditation Program (AAP) certified laboratories that are on contract: SuperSamplelab, Inc., Concrete Lab Associates, or Concrete Testing Company.
2.3.2 List of Verification Tests and Frequencies
Table 12 presents a list of Source Inspection materials verification testing and frequencies that will be implemented in this project, where applicable.
Table 10: List of Source Inspection Material Verification Tests and Frequencies
Bid # |
Bid Item |
Material |
Amount/Samples of Material to be Tested |
Tests Performed |
60 |
PTFE Bearing |
PTFE Spherical Bearing |
Lot of bearings and number of samples defined in the special provisions |
ASTM D4014, ASTM D4894, ASTM D4895, ASTM A709, ASTM A240, Type 304, A1011GR.36, AWS D1.6, AWS D1.1 |
61 |
Structural Concrete Bridge |
Concrete |
Review of QC test data only |
ASTM C 150, ASTM C 494, ASTM C 260, ASTM C 618 |
Steel reinforcement |
1 sample from rebar supplier at start of production |
ASTM A706, ASTM A615 |
Elastomeric Bearing |
One per lot or batch (whichever is greater) |
ASTM D4014, CT 663 |
Steel reinforcement Welding |
Min 25% of production lot |
AWS D1.4 |
63 |
Structural Concrete, Approach Slab |
Epoxy Coating |
1 QA sample selected from each epoxy coater as a check sample |
ASTM A775, ASTM A884, ASTM A934 |
66 |
Precast Concrete Girders |
Strand |
1 QA sample per 2 strand packs |
ASTM A421, ASTM A916, ASTM A722 |
Steel reinforcement |
1 sample from rebar supplier at start of production |
ASTM A706, ASTM A615 |
Concrete |
Per table 10 footnote, 1 sample for aggregate and SCM |
ASTM C 150, ASTM C 494, ASTM C 260, ASTM C 618 |
69 |
Soundwall (Masonry Block) |
Masonry Block High Strength |
1 per 10,000 blocks |
UBC 2404, ASTM C140 |
71 |
Steel Pipe Piles Class N |
Welding |
Per AWS D1.1 and Project Specials - 25% QA UT |
Priority 1a item. Frequency of inspection will be per 2.2.4.1 and will include UT testing and visual per special provisions. |
74 |
Structural Steel |
High strength Fasteners, Anchorage |
See Table 2.2.4.1 for bolt sampling frequency |
ASTM A325, ANSI/ASME B1.2, ASTM A370, ASTM B499, ASTM E8, ASTM E10, ASTM E18, ASTM F606, ASTM F1554/A307, ASTM A751 |
Welding |
QA to perform random checks of field welding operations |
Appropriate NDT verification UT, VT, MT, AWS D1.5 per project specials. |
Galvanizing |
No QA source samples for Galvanizing |
Verify QC records for ASTM A123 |
75 |
Furnish Sign Structure (Truss) |
Anchorage |
Sampling per section 2.2.4.1 |
ASTM F1554/A307, ASTM A370, ASTM F606, ASTM A751 |
Welding |
See 2.2.4.1 and table 10 |
Appropriate NDT verification UT, VT, MT, per project specials. |
Galvanizing |
No QA source samples for Galvanizing |
ASTM A123 |
76 |
Furnish Formed Panel Sign |
Sign Panel |
Priority 2 item. Inspection per 2.2.4.1. No physical samples except verification of QC records. |
ASTM B209, 5052-H32, ASTM B449, ASTM D4956 |
80 |
Precast Piles |
Strand |
1 QA sample per 2 strand packs |
ASTM A421, ASTM A916, ASTM A722 |
Steel reinforcement |
1 sample from rebar supplier at start of production |
ASTM A706, ASTM A615 |
Concrete |
Per table 10 footnote, 1 sample for aggregate and SCM |
ASTM C 150, ASTM C 494, ASTM C 260, ASTM C 618 |
84 |
Miscellaneous Iron and Steel |
Anchorage |
Sampling per section 2.2.4.1 |
ASTM F1554/A307, ASTM F606, ASTM A751 |
Source Welding |
Priority 2 item. Inspection per 2.2.4.1 |
Appropriate NDT verification UT, VT, MT, per Project Special. |
Galvanizing |
No QA source samples for Galvanizing |
ASTM A123 |
101 |
Modify Lighting and Sign Illumination |
Poles |
Priority 2b item. Inspection per 2.2.4.1 |
Appropriate NDT verification UT, VT, MT, per Project Special. |
Anchorage |
Sampling per section 2.2.4.1 |
ASTM F1554/A307, ASTM A370, ASTM F606, ASTM A751 |
Galvanizing |
No QA source samples for Galvanizing |
ASTM A123 |
2.3.3 Verification Material Filing System
The verification material filing system follow the procedures described in Sections 2.2.8.2 and 2.2.8.4 of this document.
2.3.4 Example Forms for Sampling and Testing
A Sample Identification Form (Sample City Form-0101 Form) is used for samples collected at the source. Test reports are developed for all samples sent for testing at the testing labs. A tracking number is assigned and a receiving date is recorded when the samples arrive at the testing lab. The format for the tracking number is SM 00-0XXX. This is broken down as: Structural Materials, the last two digits of the year, and the number of the sample. Testing results are E-mailed or faxed to the name listed on the Sample City Form-0101 for the material.
2.3.5 Verification/QC Testing Laboratory Conflict of Interests
Sample City’s verification and testing facilities are independent testing laboratories that are owned and operated by Sample City which only performs verification testing.
2.4 Contractor Quality Control Plans
The Sample City Materials Division will receive and review Quality Control Plans as required by the specifications. Plans are required for the following bid items:
Welding Quality Control Plans:
Bid Item 60, PTFE Spherical Bearings
Bid Item 71, Steel Pipe Piles (Class N)*
Bid Item 74, Miscellaneous Bridge Metal
Precast Quality Control Plan (PCQCP):
Bid Item 66, Precast I Girders
Bid Item 80, Precast Piles
Paint Quality Work Plan (PQWP):
Bid Item 60, PTFE Spherical Bearings
Sign Quality Control Plan:
Bid Item 76, Formed Sign Panel
* Requires QC personnel performing UT to have passed the Caltrans Transportation Laboratories written and practical examinations for UT. Sample City will verify that QC personnel are meeting this requirement.
2.4.1 Review of QC Plans
After receiving each QC Plan from the Contractor, Sample City’s RE transmits the QC plan to Sample City’s Materials Division for review. Sample City’s Materials Division has ten days to review each package, and three days for each subsequent addendum. Upon completion of the review, Sample City’s Materials Division provides the RE with its recommendations. Finally, the RE’s office will write a letter to the Contractor based on the Sample City Materials Division’s recommendations.
For bid items specified under the “Welding Quality Control” subsection of the specifications, it is required that a Welding Quality Control Plan (WQCP) be submitted to the Sample City Materials Division prior to commencing any welding. The WQCP serves as the Guiding document for the QA and QC inspectors at the fabrication facilities with regard to which welding procedures, electrodes, and welders are approved for use.
A Precast Quality Control Plan (PCQCP) is a required document for bid items specified under “Precast Quality Control” of the specifications. These plans must be submitted and approved by Sample City’s Materials Division prior to commencing any precasting
Paint Quality Work plans will be required as noted under section 4.1 and will serve as the guiding document for painting operations. These plans must be submitted and approved by Sample City’s Materials Division prior to commencing any painting.
Sign Quality Control plans are required for laminated and/or formed sign panels. These quality plans will be reviewed to ensure that the fabricator has a method of inspecting signs for compliance with the specifications.
2.4.2 Pre-Operation Meetings
Prior to submitting a Quality Control Plan (WQCP, PCQCP, or PQWP), a meeting between the Structural Materials Representative, Resident Engineer, the Contractor's QCM, and a representative from each entity performing welding and inspection operations for this project, will be held to discuss the requirements. At the option of the RE, the meeting may be held by teleconference, in person, or by video conference.
The SMR will prepare a meeting handout and lead the meeting.
The following is a summary of topics that are generally included in the agenda for discussion:
- Review Bid Items and the scope of work
- Discuss inspection coordination and schedule
- Define roles and responsibilities
- Review contract requirements related to the welding, pre-casting, or painting work
- Requirements for the WQCP, PCQCP, or PQWP
- Reports and Release Documents
- Final comments and concerns
The SMR will file the minutes per Section 2.2.8.4 of this document and distribute it to the parties that attended the meeting. A copy will be available to the OSMR upon request or audit.
2.4.2.1Shop drawings, CCOs, and RFIs
For items in which shop drawings are required, the Sample City RE will review and accept the shop drawings. A copy of the accepted shop drawings will be provided to the Sample City Materials Division personnel prior to the start of fabrication. At a minimum, the accepted shop drawings are required prior to fabrication for the following items:
- Bid Item 60 - PTFE Spherical Bearings
- Bid Item 66 - Concrete I Girders
- Bid Item 71- Steel Pipe Piling
- Bid Item 74 - Misc. Bridge Metal
- Bid Item 75 - Furnish Sign Structure
- Bid Item 80 - Pre-Cast Concrete Piles
- Bid Item 101 - Modify Lighting and Sign Illumination
2.5 Issue Resolution
Issues that arise during the QA inspection will be handled at the lowest possible level and elevated according to the organizational chart and timelines found in the Project Cooperative Agreement. Formal documentation for issue resolution including Requests for Information (RFIs) and Non-Conformance Reports (NCRs) will be handled through the following procedures:
2.5.1 CCOs, RFIs, and NCRs
RFIs are formal requests for additional information or clarification regarding the design and construction of the project which may be initiated by anyone associated with the project. An RFI is not a request to change the design; it is only to clarify features or the intentions for the existing design. A response to an RFI that changes the design may require the issuance of a Contract Change Order (CCO). The SMR must be made aware of these items in order to properly manage the Materials related items on the project. The SMR is also responsible for distributing such information to QA (Sample City) source inspectors.
The SMR needs to be informed of the approved CCO, RFI, or other revisions to the project plans and specifications that may affect Source Inspection Procedures. As such, for Materials related CCO’s, RFI’s, and changes to the plans or specifications, the SMR will be copied on correspondence and in attendance at meetings related to materials. The SMR will be copied on any materials related items at the same time or prior to issuance to the Contractor.
Nonconforming conditions identified on material, equipment, or product of in-process or completed work will be tracked on a Non-Conformance Report. The tracking of NCRs will ensure that nonconforming conditions are resolved and will prevent the incorporation of non-conforming items into the completed project. This control provides for the identification, documentation, segregation (when practical), evaluation, and disposition of the condition, notification to those concerned and who is accountable for each.
2.5.2 Instances Requiring NCRs Materials:
2.5.2.1 NCR on Product
Verification Inspectors will write an NCR on the product under the following circumstances:
- A QA inspector identifies materials that do not meet contract requirements, and the Contractor’s quality control (QC) personnel have already accepted the material.
- A QA Inspector will write an NCR for the material if the contractor cannot correct the deficiency within a work shift.
- Note: QA Inspector will typically not write an NCR on a material that will be corrected within a work shift and the non-conformance is not repeated.
- QA Inspection reveals obvious attempts to hide processes or products that do not meet the contract requirements.
- Contractor ships material without a Field/COC release tag.
QA Inspectors will typically not write an NCR on Material under the following circumstances:
- Material that has not been inspected and accepted by the contractor’s QC personnel.
- Material that can be repaired or fixed within a work shift of when the deficiency is discovered (an NCR may be required on the QC, see procedures outline above).
- Material that has been identified by QC that does not meet the contract requirements and can be repaired during production. (This conversation and action will be noted in the inspection report by the Verification inspector).
- Rejectable discontinuities found through nondestructive testing by QA Inspector in areas not tested by QC and repairs are commenced promptly (this conversation and action should be noted in the inspection report by the Verification Inspector).
2.5.2.2NCR on QC Personnel/Process
Verification Inspectors will write an NCR on the Quality Control Personnel under the following circumstances:
- A QA Inspector identifies material that does not meet contract requirements, and the contractor’s quality control (QC) personnel have already accepted the material.
- The third occurrence of the same deficiency regardless of the contractor’s ability to correct the problem within a work shift (repeated from above).
- Note than an NCR is not required on the first or second occurrences of a deficiency if QC personnel acknowledge the problem and ensure it is corrected within a work shift.
- Any non-conforming item that is a repeat of a previous item that resulted in an NCR.
- Any action taken by QC that is not in conformance with the contract requirements or any attempts to hide nonconforming items.
2.5.2.3 NCR Procedure Details
QA Inspectors will ensure the following procedures are met when dealing with NCRs:
- The inspector locates a problem or deficiency and informs QC and/or a responsible representative from the contractor of the issue. QA Inspectors are not authorized to stop work. QA Inspectors will identify the Contractors areas of non-conformance; however, NCRs will not be provided to the contractor or quality control personnel by the QA inspector.
- The inspector contacts his Lead Inspector to discuss the issue:
- Lead Inspector agrees that an NCR is required.
- Lead Inspector informs the SMR of the NCR who will notify the Implementing Agency RE.
- The SMR will forward the NCR to the RE
2.5.2.4 NCR Resolutions
Once non-conformances are identified and reported, the disposition and corrective action to bring the condition back into conformance will be evaluated by the Sample City RE. Potential resolutions to non-conformances include:
- Rework to meet the originally specified requirements
- Repair to achieve fitness for use
- Accept the conditions as is (require a CCO)
- Reject the condition by removing it and replacing it with material meeting the specified requirements
- Fit for purpose evaluation; blue-tag as described in 2.5.4.1 below.
An inspector or SMR will complete a Sample City Form-16 when the issue is resolved based on the list above.
2.5.2.4.1 Fit-For-Purpose Evaluation (Blue Tag Release Procedure)
The alternative fit-for-purpose evaluation and blue tag release process will allow the QA Inspectors to release the material when the Sample City RE determines that the material is suitable for its intended purpose on the project but does not meet all of the contract requirements. The fit-for-purpose may be initiated by NCR, RFI, submittals, shop drawings, Contractor requests, observations, meetings, or other forms of revisions.
For fit-for-purpose releases, the Sample City RE will provide written notification to the SMR. The SMR will then notify the QA Inspector. In such cases, the QA Inspector will release the material with a blue tag and will issue a “Sample City Form-6014” Report of Verification of Material form. The Sample City Form 6014 will contain the SMR’s written recommendation as a supporting document.
2.5.3 Procedures for Handling Disagreements
Every effort will be made to resolve disputes between Owner’s and Contractor’s inspection staff at the lowest level, and will be elevated according to the organization chart and timelines found in the project charter established during the initial partnering meeting.
3 Reporting Verification Inspection Status to Implementing Agency, Sample City
3.1 Monthly Summary Report
On the first day of each month Sample City’s SMR will prepare a summary report that describes the Materials Source Inspection activities performed for the prior period. At minimum, the following topics will be discussed in the report:
- A Statement verifying continued compliance with the SIQMP signed by the Sample City RE.
- A response to any Caltrans audit findings
- A summary of the verification source inspection work completed over the reporting period and summary of work anticipated in the next period.
- A summary of NCR’s issued and the status of those outstanding
- A summary of any changes to the plans or specifications.
The report will be reviewed and verified by the Sample City RE before distribution to the Caltrans Oversight SMR.
Sample City understands that individual inspection reports are not required to be submitted with the monthly summary report. Sample City will file the inspection and other reports per Section 2.2.8.4 of this document and will make them available for audits.
3.2 Final Acceptance Letter
Upon completion of all work, the Sample City RE will provide the Caltrans Oversight RE and oversight SMR with a stamped letter stating that these approved SIQMP procedures were followed during the life of the project.
Back to Table of Contents
Appendix 7.
RISK ASSESSMENT FORM DEVIATING FROM HIGH RISK ITEM
Back to Table of Contents
Appendix 8.
OSM FORMS
Form |
Name |
CEM-3101 |
Notice of Materials to be Used |
TL-15 |
Quality Assurance Nonconformance Report |
TL-16 |
Quality Assurance Nonconformance Resolution |
TL-20 |
Review of Contractor's Submittal |
TL-21 |
Review of Welder Qualifications |
TL-22 |
Review of Contractor's Paint QWP |
TL-23 |
Review of Contractor's Welding QCP |
TL-24 |
Welding QCP NCR |
TL-25 |
Review of Contractor's Welding QCP |
TL-26 |
Welding FCP NCR |
TL-27 |
Review of Contractor's WPS/PQR |
TL-28 |
Notice of Materials to be Inspected |
TL-29 |
Report of Inspection Materials |
TL-38 |
Inspection Request |
TL-608 |
Notice of Materials to be Furnished |
TL-649 |
Verification of Materials on Hand |
TL-6011 |
Notice of Shipment Material |
TL-6012 |
Report of Inspection of Stock Material |
TL-6014 |
Material Suitability Report |
TL-6031 |
Welding Inspection Report |
TL-6032 |
Welding Fitness Report |
TL-6033 |
Concrete Inspection Report |
TL-6034 |
Source Inspection Report |
TL-6035 |
QA Lead Verification Report |
TL-6037 |
Weekly Fabrication Report |
TL-6040 |
Document Distribution |
TL-6041 |
Report of Drawing Review |
TL-6042 |
Paint Inspection Report |
Note: OSM Forms are including in this Manual only as guidance for Local Agencies, Caltrans and OSM logos should be replaced with Local Agency logos and Local Agency statement of work language
CEM 3101 NOTICE OF MATERIALS TO BE USED
IMAGE
TL-15 QUALITY ASSURANCE NONCONFORMANCE REPORT
IMAGE
TL-16 QUALITY ASSURANCE NONCONFORMANCE RESOLUTION
IMAGE
TL-20 REVIEW OF CONTRACTOR'S SUBMITTAL
IMAGE
TL-21 REVIEW OF WELDER QUALIFICATIONS
IMAGE
TL-22 REVIEW OF CONTRACTOR'S PAINT QWP
IMAGE
IMAGE
TL-23 REVIEW OF CONTRACTOR'S WELDING QCP
IMAGE
IMAGE
TL-24 WELDING QCP NCR
IMAGE
TL-25 REVIEW OF CONTRACTOR'S WELDING FCP
IMAGE
TL-26 WELDING FCP NCR
IMAGE
TL-27 REVIEW OF CONTRACTOR'S WPS/PQR
IMAGE
TL-28 NOTICE OF MATERIALS TO BE INSPECTED
IMAGE
TL-29 REPORT OF INSPECTION OF MATERIALS
IMAGE
TL-38 INSPECTION REQUEST
IMAGE
TL-608 NOTICE OF MATERIALS TO BE FURNISHED
IMAGE
TL-649 VERIFICATION OF MATERIALS ON HAND
IMAGE
TL-6011 NOTICE OF SHIPMENT OF MATERIAL
IMAGE
TL-6012 REPORT OF INSPECTION OF STOCK MATERIAL
IMAGE
TL-6014 MATERIAL SUITABILITY REPORT
IMAGE
TL-6031 WELDING INSPECTION REPORT
IMAGE
TL-6032 WELDING FITNESS REPORT
IMAGE
TL-6033 CONCRETE INSPECTION REPORT
IMAGE
TL-6034 SOURCE INSPECTION REPORT
IMAGE
TL-6035 QA LEAD VERIFICATION REPORT
IMAGE
TL-6037 WEEKLY FABRICATION REPORT
IMAGE
TL-6040 DOCUMENT DISTRIBUTION
IMAGE
TL-6041 REPORT OF DRAWING REVIEW
IMAGE
TL-6042 PAINT INSPECTION REPORT
IMAGE
Back to Table of Contents
Appendix 9.
TABLE OF MATERIAL SAMPLING FREQUENCIES AND TESTING REQUIREMENTS
This table is not all encompassing, and is intended as a guide. Project documents have a higher precedence than this table. This table provides the minimal QA level of inspection and testing required. The Local Agency can always provide a higher/more intensive level of QA based on their analysis. All source inspection |
|
|
|
|
|
Type of Material |
Source Inspection |
Sampling Frequency |
Type of Test/Standard to Verify |
Comments |
Electrical Material |
Service Enclosures |
Yes |
100% |
QA Verification of Standard Specification and Special Provision Requirements |
Most likely can be inspected at the source with portable equipment. Note: 100% post installation - field testing also required. |
Lighting Controls |
Yes |
100% |
QA verification of Standard Specification and Special Provision Requirements |
Most likely can be inspected at the source with portable equipment. Note: 100% post installation - field testing also required. |
Sign Controls |
Yes |
100% |
QA verification of Standard Specification and Special Provision Requirements |
Most likely can be inspected at the source with portable equipment. Note: 100% post installation - field testing also required. |
Battery Backup System Cabinets |
Yes |
100% |
QA verification of Standard Specification and Special Provision Requirements |
Most likely can be inspected at the source with portable equipment. Note: 100% post installation - field testing also required. |
Telephone Demarcation Cabinets |
Yes |
100% |
QA verification of Standard Specification and Special Provision Requirements |
Most likely can be inspected at the source with portable equipment. Note: 100% post installation - field testing also required. |
LED Extinguishable Message Signs |
Yes |
100% |
QA verification of Standard Specification and Special Provision Requirements |
Most likely will be sent to a lab unless specialized portable equipment is available. Note: 100% post installation - field testing also required. |
Accessible Pedestrian Systems |
Yes |
100% |
QA verification of Standard Specification and Special Provision Requirements |
Most likely can be inspected at the source with portable equipment. Note: 100% post installation - field testing also required. |
334 Cabinets |
Yes |
100% |
QA verification of Standard Specification and Special Provision Requirements |
334 cabinets used to control traffic is State Furnished. 334 cabinets used for other purposes will most likely be inspected at the source with portable equipment. Note: 100% post installation - field testing also required. |
Luminaires |
Yes |
Per 2010 RSS and 2015 SS & RSS |
QA verification of Standard Specification and Special Provision Requirements |
Most likely will be sent to a lab unless specialized portable equipment is available. Note: 100% post installation - field testing also required. |
LED Signal Traffic Modules & LED Signal Modules for Flashing Beacon Controllers |
Yes |
Per 2010 RSS and 2015 SS & RSS |
QA verification of Standard Specification and Special Provision Requirements |
Most likely will be sent to a lab unless specialized portable equipment is available. Note: 100% post installation - field testing also required. |
Pedestrian Countdown Modules |
Yes |
Per 2010 RSS and 2015 SS & RSS |
QA verification of Standard Specification and Special Provision Requirements |
Most likely will be sent to a lab unless specialized portable equipment is available. Note: 100% post installation - field testing also required. |
Closed Circuit TV Cameras |
No |
NA |
Certificate of Compliance |
RE/SR must verify COC at the jobsite. Note: 100% post installation - field testing also required. |
Sign Light Fixtures |
No |
NA |
Certificate of Compliance |
RE/SR must verify COC at the jobsite. Note: 100% post installation - field testing also required. |
Flashing Beacon Controller Assemblies (not including LEDs) |
No |
NA |
Certificate of Compliance |
RE/SR must verify COC at the jobsite. Note: 100% post installation - field testing also required. |
HAR Radio Systems |
No |
NA |
Certificate of Compliance |
RE/SR must verify COC at the jobsite. Note: 100% post installation - field testing also required. |
Modems |
No |
NA |
Certificate of Compliance |
RE/SR must verify COC at the jobsite. Note: 100% post installation - field testing also required. |
Microwave Vehicle Detection Systems |
No |
NA |
Certificate of Compliance |
RE/SR must verify COC at the jobsite. Note: 100% post installation - field testing also required. |
Video Vehicle Detection Systems |
No |
NA |
Certificate of Compliance |
RE/SR must verify COC at the jobsite. Note: 100% post installation - field testing also required. |
Battery Backup System Batteries |
No |
NA |
Certificate of Compliance |
RE/SR must verify COC at the jobsite. Note: 100% post installation - field testing also required. |
Conduit |
No |
NA |
Certificate of Compliance |
RE/SR must verify COC at the jobsite. Note: 100% post installation - field testing also required. |
Conductors |
No |
NA |
Certificate of Compliance |
RE/SR must verify COC at the jobsite. Note: 100% post installation - field testing also required. |
Cable |
No |
NA |
Certificate of Compliance |
RE/SR must verify COC at the jobsite. Note: 100% post installation - field testing also required. |
Fiber Optic Equipment |
No |
NA |
Certificate of Compliance |
RE/SR must verify COC at the jobsite. Note: 100% post installation - field testing also required. |
Fiber Optice Cable |
No |
NA |
Certificate of Compliance |
RE/SR must verify COC at the jobsite. Note: 100% post installation - field testing also required. |
Loop Wire |
No |
NA |
Certificate of Compliance |
RE/SR must verify COC at the jobsite. Note: 100% post installation - field testing also required. |
Pull Boxes |
No |
NA |
Certificate of Compliance |
RE/SR must verify COC at the jobsite. Note: 100% post installation - field testing also required. |
Splice Vaults |
No |
NA |
Certificate of Compliance |
RE/SR must verify COC at the jobsite. Note: 100% post installation - field testing also required. |
Structural Materials (All references in the "Type of Test/Standard to Verify" column refers to the 2010 Standard Specification unless otherwise noted. The corresponding QASI manual section can also be references for more guidance. Local Agency to verify RSS or Special Provisions for changes to standard requirements. |
Fasteners |
High Strength Bolts |
Yes |
55-G QASI Manual |
55-1.02A(1); 55-1.01D(3)(b) |
Material sampling and testing including galvanizing and visual inspection; witness rotational capacity testing and document in inspection reports |
High Strength Cap Screws |
Yes |
55-G QASI Manual |
86-2.04B(2) |
Material sampling and testing including galvanizing and visual inspection |
Anchor Bolts |
Yes |
55-G QASI Manual |
55-1.02A(1) |
Material sampling and testing including galvanizing and visual inspection |
Nuts used with High Strength Bolts & Anchor Bolts |
Yes |
55-G QASI Manual |
55-1.02A(1) |
Material sampling and testing including galvanizing and visual inspection |
Washers used with High Strength Bolts & Anchor Bolts |
Yes |
55-G QASI Manual |
55-1.02A(1) |
Material sampling and testing including galvanizing and visual inspection |
Bearings |
Elastomeric bearing pads (plain reinforced) |
No |
(1) 8x12 in sample per lot |
51-3.02A(4)(c); 51-3.02B(2) |
Samples may be selected by Engineer or sent in by fabricator |
Elastomeric bearing pads (steel reinforced) |
No |
(1) 8x12 in sample per lot |
51-3.02A(4)(c); 51-3.02B(2) |
Samples may be selected by Engineer or sent in by fabricator |
PTFE Bearings |
Yes |
Per special provisions |
See project special provisions & QASI manual section 51-D |
CWI; SMR must accompany inspector on source inspections |
Reinforcement |
Epoxy Coating Powder |
No |
1 per batch |
52-2.01A(3)(b) and 52-2.01A(3)(c) |
|
Epoxy coated reinforcement (green or purple) |
Yes |
Per 52-2.02A(4) or 52-2.03A(4) |
52-2.02A(4) or 52-2.03A(4) |
|
Epoxy coated dowel bars & tie bars (includes baskets) |
Yes |
QASI Manual Section 40-C |
40-1.02E (tie bars); 40-1.02F (dowel bars); 40-1.02G (baskets) |
|
Stainless Steel Reinforcement |
Yes |
52-4 |
52-4 |
|
Headed Bar Reinforcement |
Yes |
52-5 |
52-5 |
|
Galvanized rebar |
Yes |
QASI Manual Section 52 |
52-3 |
|
Reinforcement splices: welded (hoops) or mechanical couplers |
Yes |
52-6.01D(5) |
ASTM A706; California Test 670; Material verification, inspection and review of welding, galvanizing, visual and dimensional inspection; See QASI manual for more detail |
|
Steel |
Structural Steel Bridge Members and Attachments |
Yes |
N/A |
55;59 |
See section 55 and 59 of the QASI manual; CWI;MT;UT |
Bridge Joint Restrainers |
Yes |
See QASI Manual Sections 75-C and 75-E |
75-1.03E |
CWI inspector required for welding inspection |
Cable Type Restrainers |
Yes |
See QASI Manual Sections 75-C and 75-E |
75-1.03E(2) |
CWI inspector required for welding inspection |
Miscellaneous iron and steel, misc. bridge metal, bearing assemblies, rings and covers, frames and grates, etc |
See QASI Manual Section 75 |
See QASI Manual Section 75 |
75 |
CWI Inspector required for welding inspection |
Painting Structural Steel |
Yes |
N/A |
See QASI Manual Section 59 |
|
Paints for Metal |
Yes |
Per Batch |
91-2 |
Must be tested before shipping to the jobsite. |
Precast Concrete |
Tier 1 & Tier 2 Precast concrete (per 90-4.01D(1)) |
Yes |
N/A |
51;90 |
See section 51 and 90 of the QASI manual; QA PCI lvl 1 for tier 1; QA PCI lvl 2 for tier 2 |
Prestressing Strand |
Yes |
50-1.01C(4) |
50-1.01D(2) |
|
Tier 3 pipes > 60 in diameter |
Yes |
QASI Manual Sections 65-8.02 |
AASHTO M 170/AASHTO T 280 (D-Load); AASHTO T 280 (Absorption Test); AASHTO T 22 (Cylinder Breaks) |
Check special provisions if all three test methods are required. At a minimum witness D-Load testing. |
Joint Seals |
Joint seal, type A and AL |
No |
51-2.02B(1)(c) |
51-2.02B(1)(d) |
|
Joint seal, type B preformed elastomeric joint seal |
Yes or sample at jobsite |
1 per lot |
51.2.02C(2) |
|
Joint seal assembly > 4" Movement Rating |
Yes |
N/A |
See 51-C of the QASI Manual |
CWI inpsector required for welding inspection; MT; UT |
Poles and Signs |
Poles: signal & lighting |
Yes |
100% |
Material verification, inspection and review of welding, galvanizing, painting, visual and dimensional inspection; See QASI manual for more detail |
CWI Inspector required |
Overhead Sign Structures |
Yes |
NA |
Material verification, inspection and review of welding, galvanizing, painting, visual and dimensional inspection |
CWI;MT;UT |
Signs: changeable message |
Yes |
NA |
Material verification, inspection and review of welding, galvanizing, painting, visual and dimensional inspection; NDT as required; see QASI manual section 56-3 |
CWI;MT;UT |
Steel Piles |
Class N Pipe Piles |
Yes |
NA |
Material verification, inspection and review of welding, galvanizing, painting, visual and dimensional inspection |
|
Steel Soldier Piles |
Yes |
100& |
Material verification, inspection and review of welding, galvanizing, painting, visual and dimensional inspection |
|
Back to Table of Contents
Appendix 10.
SAMPLE IDENTIFICATION CARD
Back to Table of Contents
Appendix 11.
LIST OF APPLICABLE INDUSTRY STANDARDS
Type of Material |
Type of Test/Standard to Verify |
Electrical Material |
Service Enclosures |
QA verification of Standard Specification and Special Provision Requirements |
Flashing Beacon Controller Assemblies |
QA verification of Standard Specification and Special Provision Requirements |
Lighting Controls |
QA verification of Standard Specification and Special Provision Requirements |
Sign Controls |
QA verification of Standard Specification and Special Provision Requirements |
Battery Backup System Cabinets |
QA verification of Standard Specification and Special Provision Requirements |
Telephone Demarcation Cabinets |
QA verification of Standard Specification and Special Provision Requirements |
LED Extinguishable Message Signs |
QA verification of Standard Specification and Special Provision Requirements |
Accessible Pedestrian Systems |
QA verification of Standard Specification and Special Provision Requirements |
334 cabinets |
QA verification of Standard Specification and Special Provision Requirements |
Closed Circuit TV Cameras |
QA verification of Standard Specification and Special Provision Requirements |
Luminaires |
QA verification of Standard Specification and Special Provision Requirements |
LED Signal Traffic Signal Modules |
QA verification of Standard Specification and Special Provision Requirements |
Pedestrian Countdown Modules |
QA verification of Standard Specification and Special Provision Requirements |
Sign Light Fixtures |
QA verification of Standard Specification and Special Provision Requirements |
HAR Radio Systems |
Certificate of Compliance |
Modems |
Certificate of Compliance |
Microwave Vehicle Detection Systems |
Certificate of Compliance |
Video Vehicle Detection Systems |
Certificate of Compliance |
Battery Backup System Batteries |
Certificate of Compliance |
Conduit |
Certificate of Compliance |
Conductors |
Certificate of Compliance |
Cable |
Certificate of Compliance |
Fiber Optic Equipment |
Certificate of Compliance |
Fiber Optic Cable |
Certificate of Compliance |
Loop Wire |
Certificate of Compliance |
Pull Boxes |
Certificate of Compliance |
Splice Vaults |
Certificate of Compliance |
Structural Material
(All references in the "Type of Test/Standard to Verify" column refers to the 2010 Standard Specification unless otherwise noted. The corresponding QASI manual section can also be referenced for more guidance. Local Agency to verify RSS or Special Provisions for changes to standard requirements)
|
Fasteners |
High Strength Bolts |
55-1.02A(1); 55-1.01D(3)(b) |
High Strength Cap Screws |
86-2.04B(2) |
Anchor Bolts |
55-1.02A(1) |
Nuts used with High Strength Bolts & Anchor Bolts |
55-1.02A(1) |
Washers used with High Strength Bolts & Anchor Bolts |
55-1.02A(1) |
Bearings |
Elastomeric bearing pads (plain reinforced) |
51-3.02A(4)(c); 51-3.02B(2) |
Elastomeric bearing pads (steel reinforced) |
51-3.02A(4)(c); 51-3.02B(2) |
PTFE Bearings |
See project special provisions & QASI manual section 51-D |
Reinforcement |
Epoxy Coating Powder |
52-2.01A(3)(b) and 52-2.01A(3)(c) |
Epoxy coated reinforcement (green or purple) |
52-2.02A(4) or 52-2.03A(4) |
Epoxy coated dowel bars & tie bars (includes baskets) |
40-1.02E (tie bars); 40-1.02F (dowel bars); 40-1.02G (baskets) |
Stainless Steel Reinforcement |
52-4 |
Headed Bar Reinforcement |
52-5 |
Galvanized rebar |
52-3 |
Reinforcement splices: welded (hoops) or mechanical couplers |
ASTM A706; California Test 670; Material verification, inspection and review of welding, galvanizing, visual and dimensional inspection; See QASI manual for more detail |
Steel |
Structural Steel Bridge Members and Attachments |
55;59 |
Bridge Joint Restrainers |
75-1.03E |
Cable Type Restrainers |
75-1.03E(2) |
Miscellaneous iron and steel, misc. bridge metal, bearing assemblies, rings and covers, frames and grates, etc |
75 |
Painting Structural Steel |
See QASI Manual Section 59 |
Paints for Metal |
91-2 |
Precast Concrete |
Tier 1 & Tier 2 Precast concrete (per 90-4.01D(1)) |
51;90 |
Prestressing Strand |
50-1.01D(2) |
Tier 3 pipes > 60 in diameter |
AASHTO M 170/AASHTO T 280 (D-Load); AASHTO T 280 (Absorption Test); AASHTO T 22 (Cylinder Breaks) |
Joint Seals |
Joint seal, type A and AL |
51-2.02B(1)(d) |
Joint seal, type B preformed elastomeric joint seal |
51-2.02C(2) |
Joint seal assembly > 4" Movement Rating |
See 51-C of the QASI Manual |
Poles and Signs |
Poles: signal and lighting |
Material verification, inspection and review of welding, galvanizing, painting, visual and dimensional inspection; See QASI manual for more detail |
Overhead Sign Structures |
Material verification, inspection and review of welding, galvanizing, painting, visual and dimensional inspection |
Signs: changeable message |
Material verification, inspection and review of welding, galvanizing, painting, visual and dimensional inspection; NDT as required; see QASI manual section 56-3 |
Steel Piles |
Class N Pipe Piles |
Material verification, inspection and review of welding, galvanizing, painting, visual and dimensional inspection |
Steel Soldier Piles |
Material verification, inspection and review of welding, galvanizing, painting, visual and dimensional inspection |
Back to Table of Contents
Appendix 12.
SIQMP APPROVAL LETTER
Back to Table of Contents
Appendix 13.
IQA AUDIT COVER LETTER
Back to Table of Contents
Appendix 14.
IQA AUDIT REPORT
Back to Table of Contents
Appendix 15.
NDT REQUIREMENT REFERENCE
Fabricated Item |
Standard Specification |
Welding Code and Ref. Standard Spec. |
Required NDT and Ref. Standard Spec. |
Remarks Other Specification References |
Structural Steel Bridge Members & Attachments |
Sec. 11 and 55 |
AWS D1.5, Sec. 11-3 Weld QC Sec. 55-1.02B(7) |
RT, UT, MT AWS D1.5, Sec. 6.7 Sec. 55-1.02B(7) |
Fracture Critical Members AWS/AASHTO or AREMA Fracture Control Plan |
Column Casings & Bridge Strengthening Steel |
Sec. 55 |
AWS D1.5 |
None - Check Spec. Provisions |
Re: Sec. 11-3 of Std. Specs. Welding Quality Control |
Shear Connectors (Studs) |
Sec. 55 and 75 |
AWS D1.5 Sec. 7 |
None |
|
Misc. Steel, Br. Metal, & Restrainers |
Sec. 75 |
AWS D1.1 |
None |
Re: Sec. 11-3 Std. Specs. Welding Quality Control |
Steel H & Pipe Piles |
Sec. 49-2.02 |
AWS D1.1 |
MT & UT for Tension Piles |
Re: Sec. 11-3 Std. Specs. Welding Quality Control |
Overhead Sign Structures |
Sec. 56-3.02L |
AWS D1.1 |
RT or UT, MT AWS D1.1 Sec. 56-3.01D(2) |
" " " |
Field Welding CJP Welds Def. Bars, Spirals & Hoops |
Sec. 52-6 |
AWS D1.4 |
RT - 25% of Joints Sec. 52-6.01D(4)(d)(ii) |
" " " |
Shop Welding, CJP & ERW Column Reinforcement |
Sec. 52-6 |
AWS D1.4 & Spec. Provisions |
None Required for Shop Welds |
" " " |
Bridge Railings |
Sec. 83-1.02 |
AWS D1.4 & Spec. Provisions |
None Required for Shop Welds |
" " " |
Signal and Lighting |
Sec. 86-2.04 |
AWS D1.1 and Spec Provisions |
None |
" " " |
Note: For welding performed by an AISC Certified Intermediate Bridges Fabricator the Standard Specifications Sec. 11-3 Welding Quality Control may not apply in its entirety. |
This table is not all encompassing of every NDT reference that may apply to a project.
Back to Table of Contents